В 2011 году Европейская комиссия оценила запасы природного газа Румынии как третье место в Европейском Союзе. В том же году большое количество этого природного газа было использовано внутри страны, поскольку Румыния импортировала всего 17% от общего потребления газа. Национальная газовая промышленность в настоящее время важна для страны с населением чуть более 21 миллиона человек, которые в значительной степени зависят от местных газовых компаний и поставщиков, а также от примерно 1,4 трлн кубометров природного газа, которые находятся под ее землей.
Elster Aeroteh играет ключевую роль в отрасли как основной производитель оборудования для измерения и регулирования газа в стране. Миллионы людей, от крупных газовых компаний до потребителей, отапливающих дома, зависят от счетчиков, регуляторов и турбин, которые они создают: Косвенно так же, как и люди, которые делают узлы регулирования газа. Поэтому, когда Elster Aeroteh приступила к выпуску новой, более простой модели регулятора давления специально для румынской промышленности, было важно, чтобы он разрабатывался и производился на месте, а не на головном предприятии компании в Германии, не только для того, чтобы быть конкурентоспособным на развивающихся рынках, но также и для обеспечения безопасности многих производственных рабочих мест компании в Румынии.
В первой части процесса инженерам Elster Aeroteh нужно было убедиться, что сборка может работать в соответствии с проектом и что ее можно точно произвести на румынском предприятии. Это означало обширные испытания под давлением, особенно на самой важной части узла - корпусе регулятора. Когда Elster Aeroteh тестировала корпус, они изначально создали прототип, созданный с помощью традиционного производства с ЧПУ… однако они обнаружили, что результаты их первоначальных испытаний были ненадежными. На самом деле, у них были проблемы даже с тем, чтобы он правильно вписался в их сборку. Такая сложная геометрия, как требуемая деталь, была просто за пределами методов ЧПУ, необходимых для получения истинной картины ее производительности.
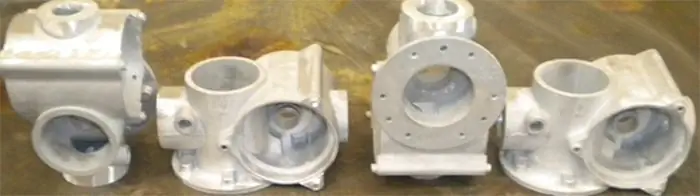
Именно тогда они обратились к LogiCAD Solutions, румынскому поставщику услуг CAD/CAM. Под руководством их технического руководителя LogiCAD было поручено быстро позволить Elster Aeroteh создать точные прототипы литых алюминиевых сплавов для этого конкретного изделия, для чего они использовали 3D-принтер 3D Systems ProJet 3510 CPX. ProJet 3510 CPX способен создавать модели литья по выплавляемым моделям RealWax с микродеталями, производя детали для широкого спектра применений, от сложных литейных приложений до изящных ювелирных изделий.
За три дня, включая подготовку к САПР, LogiCAD напечатал четыре пробных восковых образца на ProJet 3510 CPX. Затем они использовали восковые детали в качестве отливок для изготовления испытательных корпусов из алюминиевого сплава. После процесса литья LogiCAD использовала станок с ЧПУ, чтобы получить номинальные размеры сборочных плоскостей и резьбы. От файла CAD до финальной тестовой части проект занял всего около 12 дней.
Скорость и экономия, с которыми LogiCAD закончил работу, помогли Elster Aeroteh быстро пройти испытания и утвердить сборку для окончательного производства. Теперь компания создает сборки, используя формы для литья, подготовленные с помощью традиционных методов производства, на основе тестовых образцов, созданных LogiCAD… Еще одна победа 3D-печати!