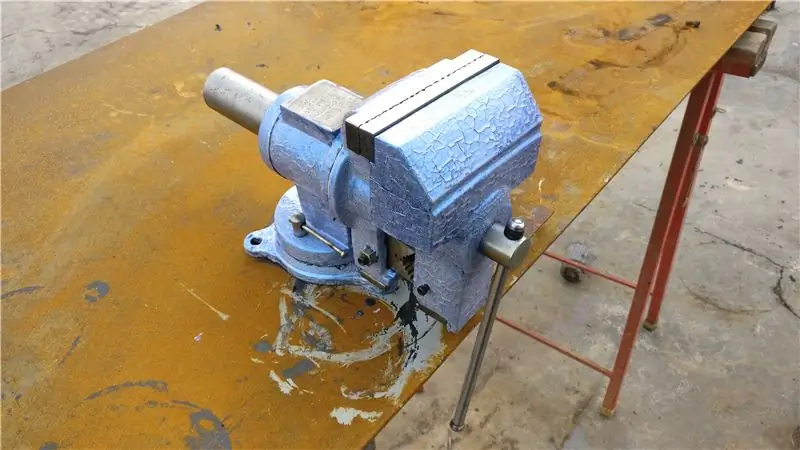
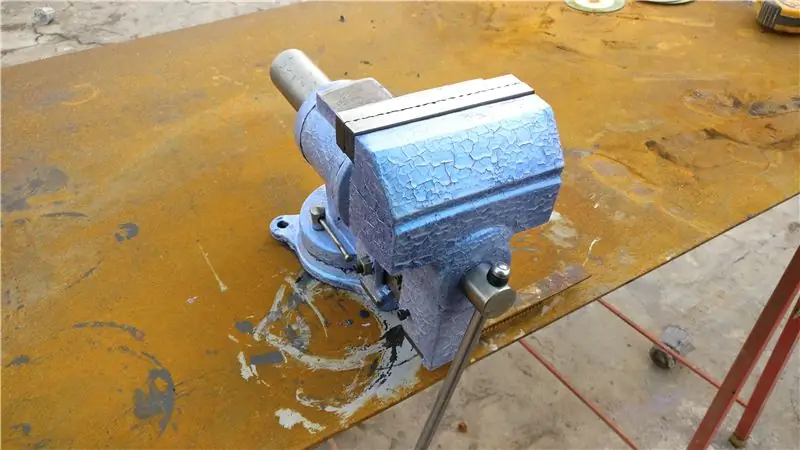
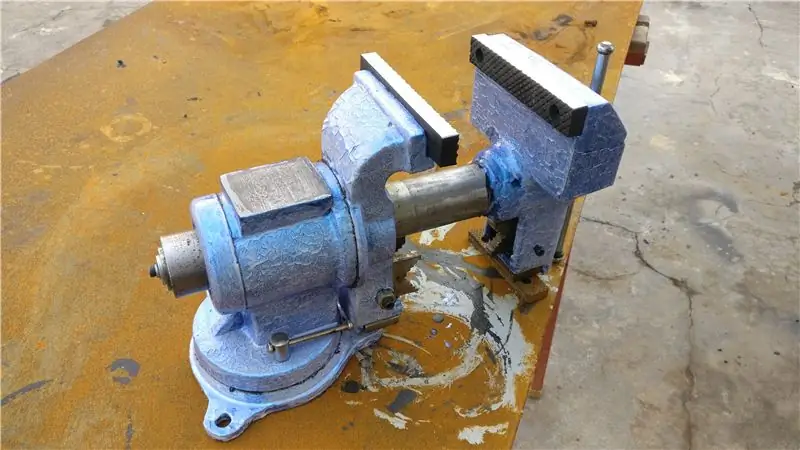
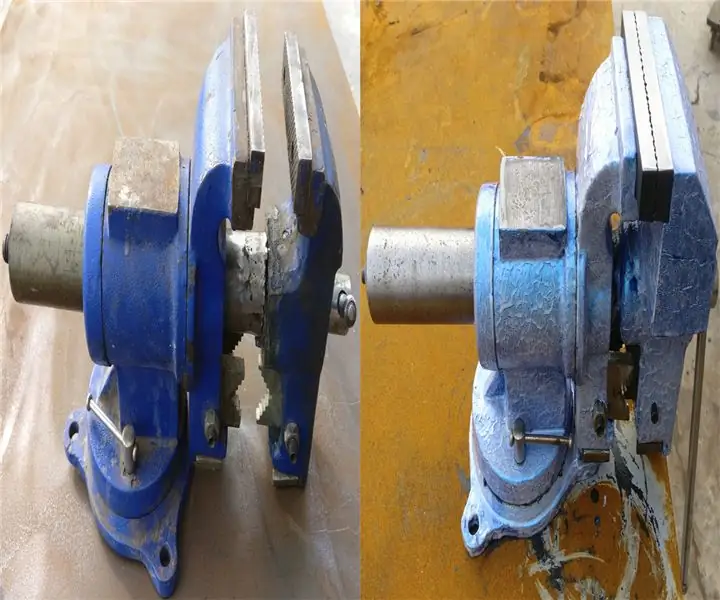
Эта инструкция посвящена тому, как мне удается сохранить свои настольные тиски. Определенно, тяжелые времена, когда я сломал эту челюсть, но я думаю, что это определенно не моя вина, что в отливке есть какой-то изъян, который приводит к катастрофическому отказу. Когда я связался с компанией по этому поводу, они сказали, что гарантия на него уже не действует, но когда я купил это в то время, они сказали, что у него 5 лет гарантии, которая теперь превратилась в 2 года, мошенник продавец. После большого спора они сказали, что могут сделать новую челюсть, но я должен заплатить половину денег. Но я очень расстроился и решил ничего не делать с продавцом, вместо этого попытался исправить это самостоятельно. В Интернете я обнаружил, что подобные проблемы возникают у многих производителей. Итак, это путешествие посвящено тому, как я исправляю свои настольные тиски за 1/4 первоначальной цены, не считая покраски. Надеюсь, это поможет вам вдохнуть новую жизнь в тиски и сэкономить деньги.
Шаг 1. Используемые материалы и инструменты
Используемые инструменты
- Сверлильный станок
- Сварочный комплект
- Сварочный электрод
- Угловая шлифовальная машина
- Откидной диск
- Шлифовальный круг
- Отбойный молоток
- Металличесая щетка
- Набор метчиков резьбы
- Набор сверл
- Набор шестигранных ключей
Используемый материал
- 2,5 дюйма в диаметре и 3 дюйма в длину
- Труба с наружным диаметром 50 мм и внутренним диаметром 30 мм (что превращается в 47 мм и 32 мм)
- Стальной пруток толщиной 10 мм
- Стальной блок 5,5 "X 3" X 2"
Шаг 2: два исправления
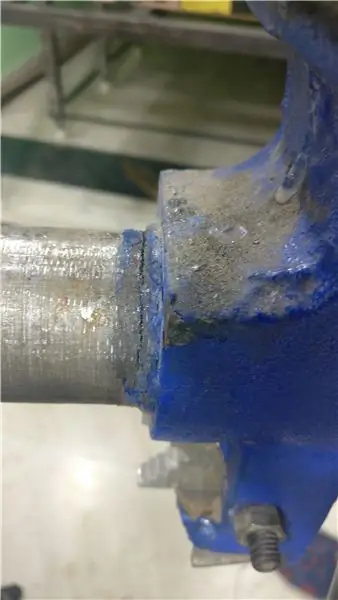
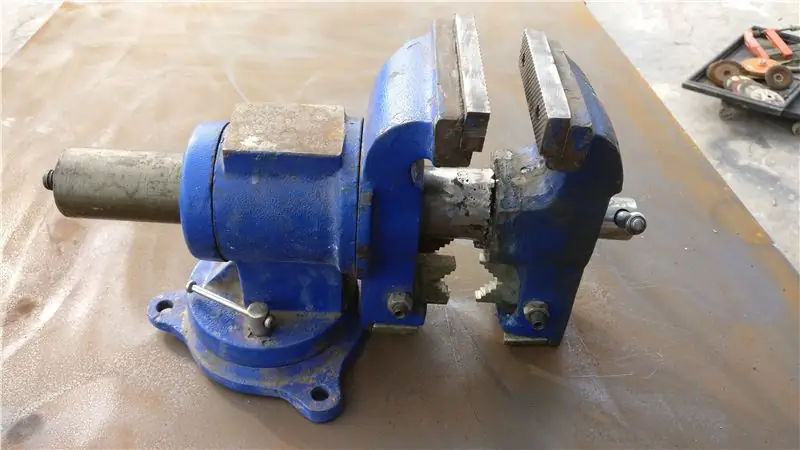
Итак, чтобы решить эту проблему, у вас есть два варианта: один - приварить его, а второй - сделать челюсть полностью из царапины, и в моем случае я пробую оба из них. Я думаю, что если я смогу спасти его с помощью простой сварки, этого никогда не произойдет, но это не сработало для меня. Я видел, как многие люди спасали свои тиски, просто выполняя сварку. Не знаю, долго это продлится или нет. Для сварки чугуна вам понадобится присадочный пруток из аналогичных материалов, и этот пруток также бывает двух типов, обрабатываемый и необрабатываемый. Я использую необрабатываемый стержень. Я провел небольшое исследование сварки чугуна в надежде, что это сработает для меня. Затем я начинаю процесс сварки, так как я сказал, что не планирую делать это руководство, и поэтому в этом руководстве нет видеозаписи сварочных работ. После окончания сварки я обнаружил, что на поверхности появляются небольшие трещинки, которых слишком много. Но сварной шов мне кажется хорошим, и я провожу испытание, сжимая челюсти, и он полностью щелкает с очень меньшим усилием. Но я не терял надежды и предпринял вторую попытку, снова сделав бороздку вокруг области сварки и начав сварку, но результат не изменился. Затем я решил сделать переднюю челюсть полностью из царапины, которая в итоге оказалась действительно прочной, и я не думал, что владелец компании сможет сделать ее настолько прочной за такую цену.
Шаг 3: Поворот основной базы передней челюсти
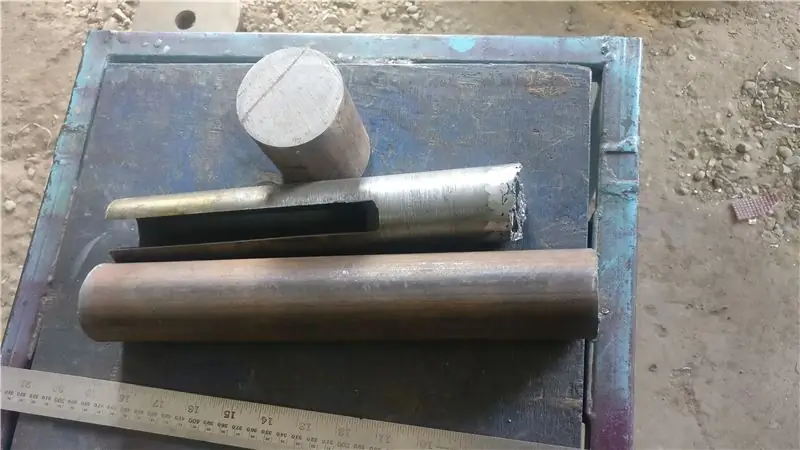
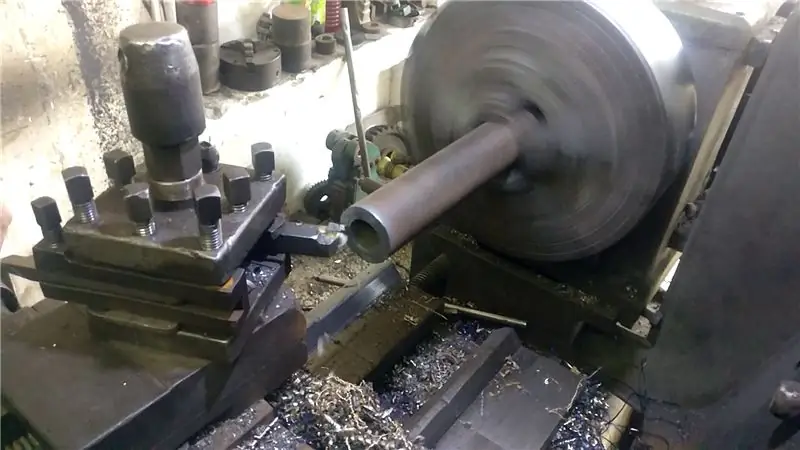
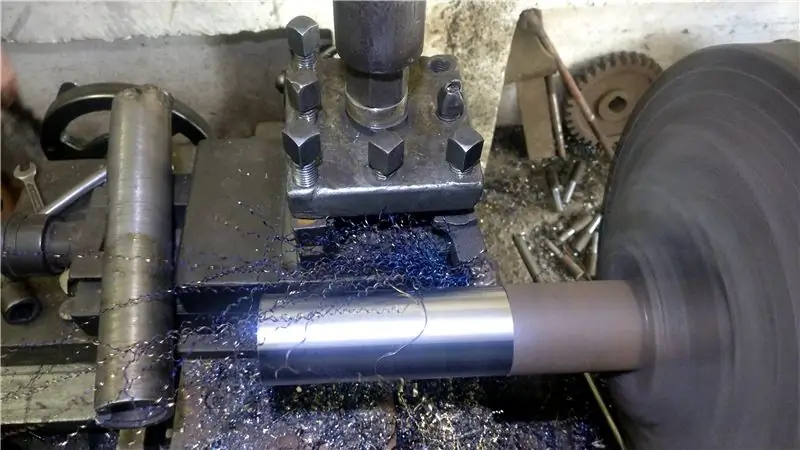
Поскольку для этого проекта у меня не было токарного станка, я обратился к токарю поблизости, который решил выполнить задание одновременно с моим приездом в его мастерскую. Поэтому для базы я покупаю два разных цилиндра. Более длинный цилиндр будет основным валом подвижной губки тисков, в который будет установлено несколько выводов, а вторые цилиндрические детали будут служить неким основанием для передней губки. В качестве материала я взял материал EN 8, который представляет собой более длинную секцию трубы, и размер, который я выбираю, измеряя размеры оригинального ствола, который был изготовлен производителем. Тернер держит эту деталь в Чаке и начинает с операции лицом к лицу. После этого он загнул внешнюю поверхность и подогнал ее до необходимого диаметра, эта операция не выполняется полностью, так как другой конец удерживается в патроне. После этого он приступает к скучным операциям, равным этой сломанной детали. После каждого прохода он продолжает проверять диаметр на предмет точных размеров. Операция наблюдения за птицами должна проводиться на некотором расстоянии, чтобы все остальное оставалось как есть. Затем он переворачивает детали и выполняет облицовку, а затем - чистку.
В качестве основания челюсти взята круглая ложа диаметром 21⁄2 дюйма длиной около 3 дюймов. Затем, после удержания, первым делом будет операция облицовки, а не небольшая работа по очистке, которая на самом деле не требуется. Затем просверливается сквозное отверстие диаметром 16 мм для ходового винта. На задней стороне есть полость, в которую вставляется этот ствол, чтобы получить более прочный сустав. Вокруг этой полости сделана фаска для захвата сварных швов для более глубокого проплавления.
Шаг 4: Соединение двух цилиндров вместе
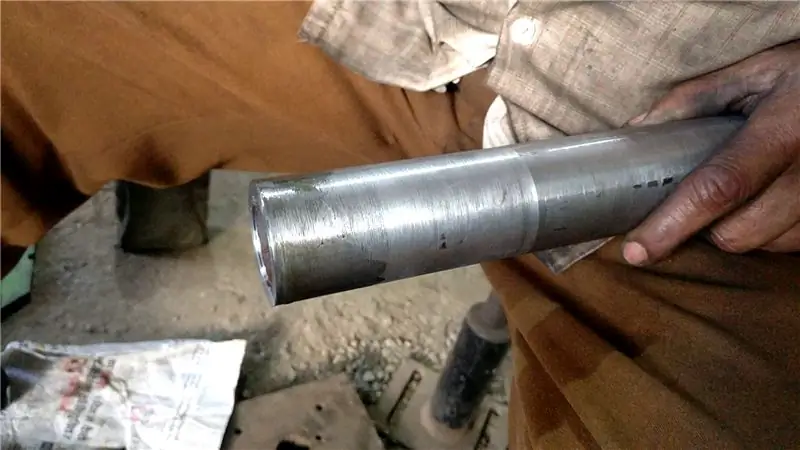
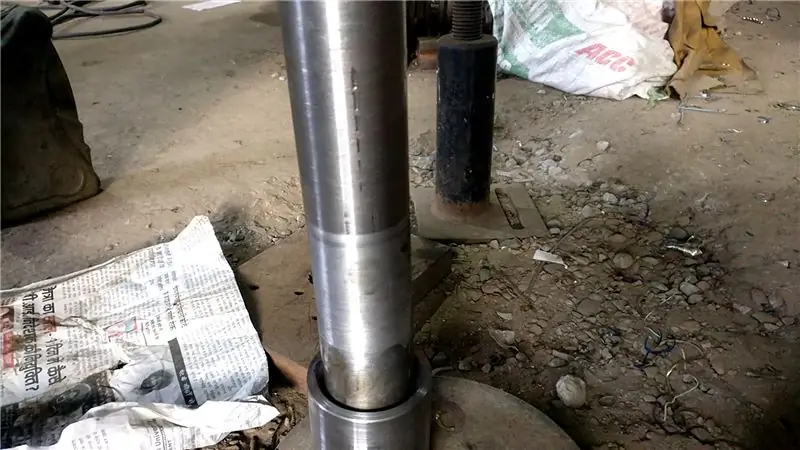
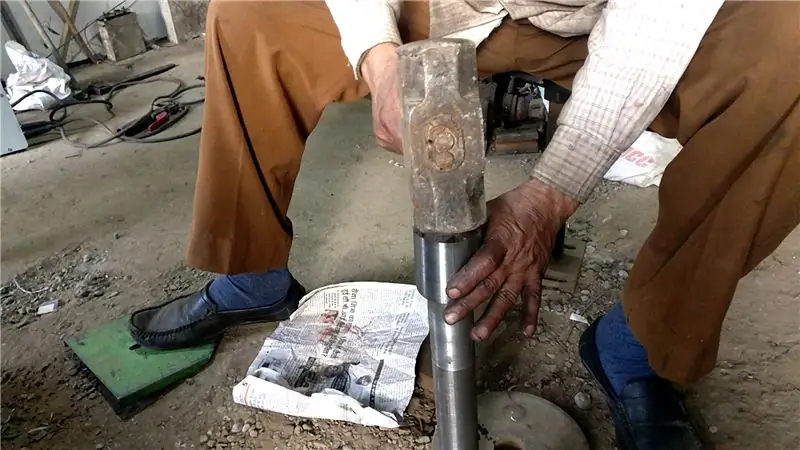
Так как внутри есть полость, в которую можно легко вставить ствол, достаточно ударить молотком. Хорошо иметь пресс для такой работы, но удары молотком тоже подойдут. Чтобы уменьшить трение, масло было растерто вокруг ствола для облегчения посадки. Как только они плотно прилегали к токарному станку, оставшуюся очистку я сделал сварной шов вокруг этой области, чтобы сделать соединение более прочным. После этого убрал лишний сварной шов и сделал стык гладким. За время сварки сделал 3-4 валика. Первый сделан на скошенной области, 2-3 немного вверх и вниз от этого первого валика. Для соединения второго и третьего валика выполняется четвертый сварной шов.
Шаг 5: Прорезание зазора для гайки
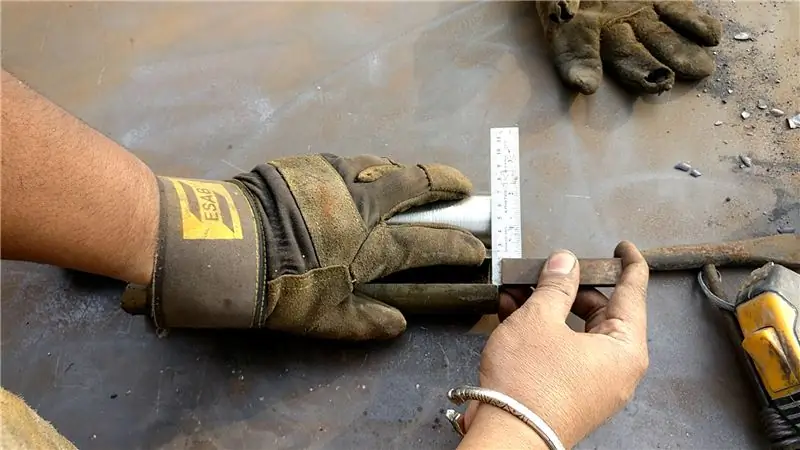
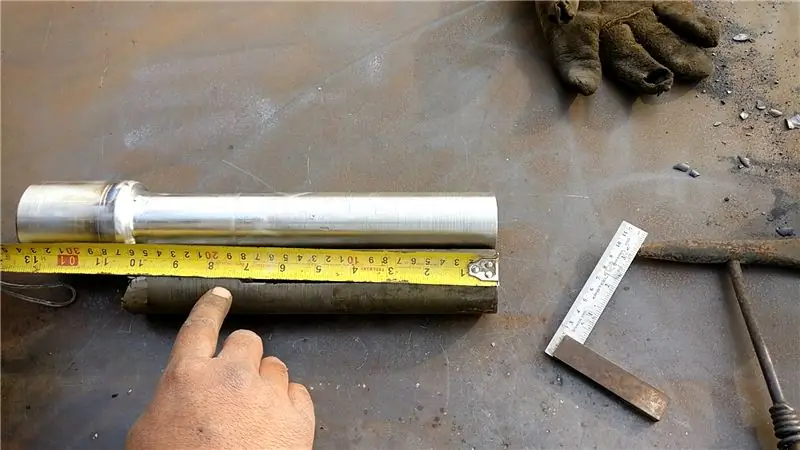
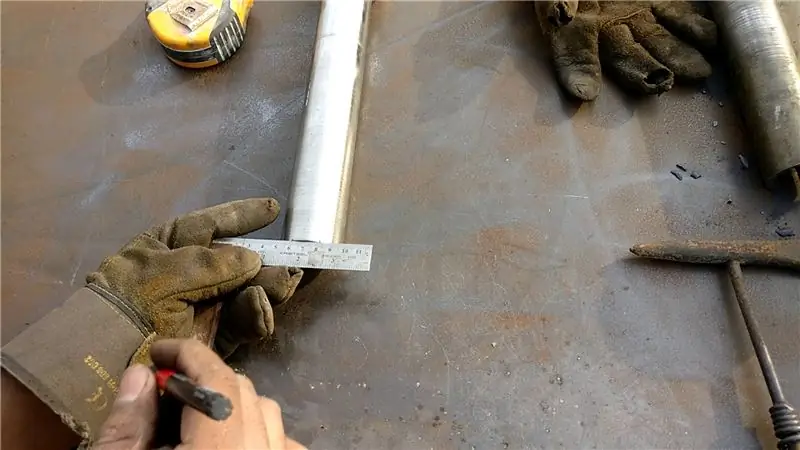
Для этого процесса я настоятельно рекомендую перенести процесс фрезерования на мельницу. Так как я этого не нашел, поэтому решил сделать это сам. Но если я найду такой, я обязательно выберу фрезерование, потому что это идеально и очень просто. Для прорези я сделал отметку, равную ширине предыдущей прорези, сделанной на этом сломанном стволе. Затем я положил это на плоскую поверхность. В моем случае я выбираю ровную мраморную поверхность, а затем делаю две линии маркером, за которыми следуют те две начальные отметки, которые я сделал ранее. Длина этого разреза составляла около 7 дюймов по мере необходимости. Затем с помощью отрезного круга удалите этот участок. Я немного уменьшил размер, чтобы можно было точно настроить его до окончательных размеров. С помощью шлифовального круга, твердосплавных борфрезов и плоского напильника этот пропил доводится до необходимой ширины. В основном это метод проб и ошибок, но фрезерование этого не требует. Как только он подходит, я перехожу к следующему этапу создания челюсти.
Шаг 6: подготовка стального блока
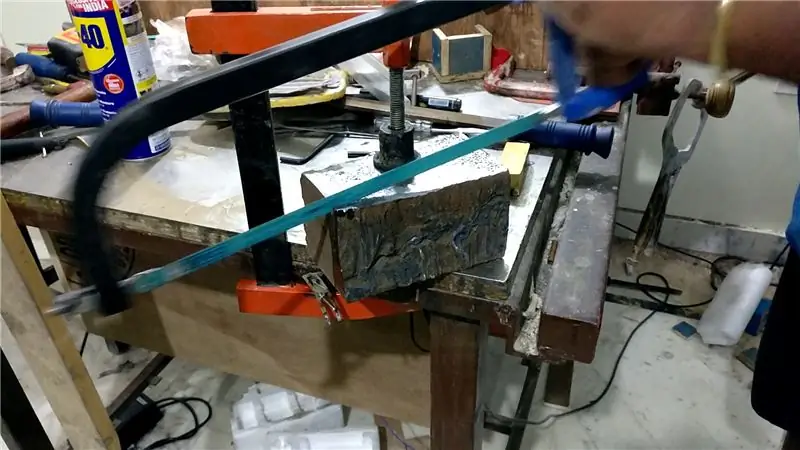
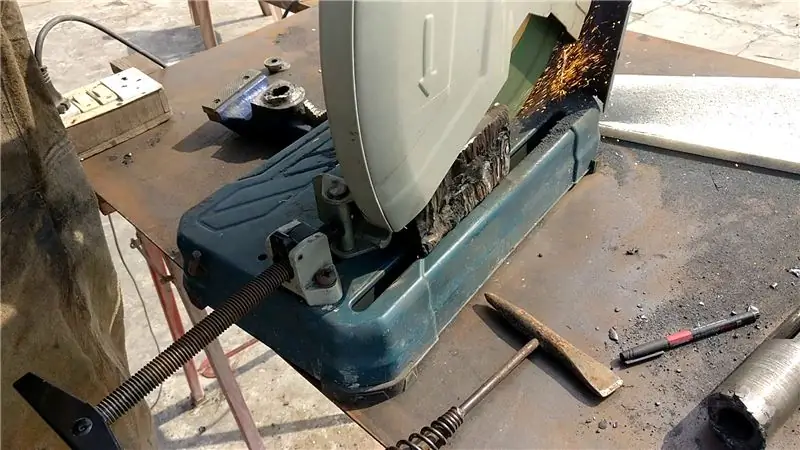
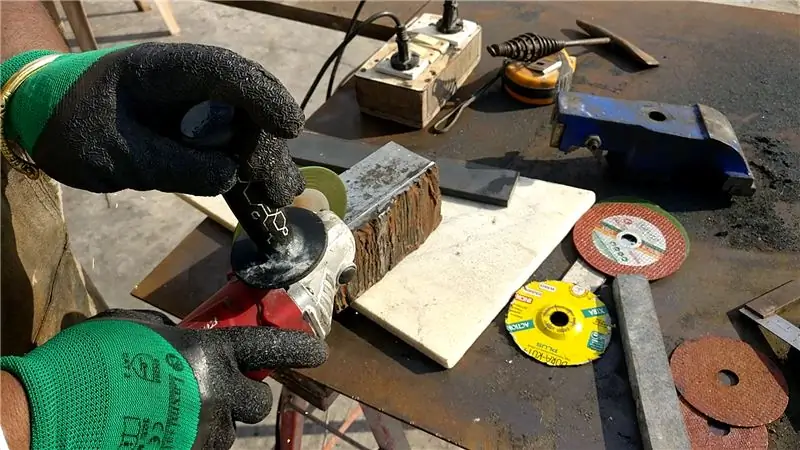
В этих тисках есть две челюсти: верхняя и нижняя. Верхняя челюсть больше по размеру, как мы видим в большинстве пороков, но нижняя челюсть немного отличается для удержания труб и других видов предметов. В качестве верхней челюсти я выбрал толстый стальной блок. Эту деталь я использовал в качестве наковальни в прошлом, но теперь у меня есть профессиональная наковальня, которую я использую, и ее больше нельзя использовать. Сначала я удаляю эту шероховатую кромку, образовавшуюся в процессе резки, с помощью кислородной горелки. Я сделал отметку ножовкой, которая ведет лезвие отрезной пилы к прямой линии, потому что отрезное колесо моей отрезной пилы всегда выходило наружу во время реза и получалось конусообразным. Этот разрез определенно помогает. Затем я начинаю чистку оставшихся сторон этого блока, и для этой чистки я не стал использовать отрезную пилу, а выбрал угловую шлифовальную машину и ножовку. В эстетических целях я сделал боковые стороны небольшим скосом 5 °, что определенно выглядит хорошо.
Шаг 7: Соединение блока и ствола вместе
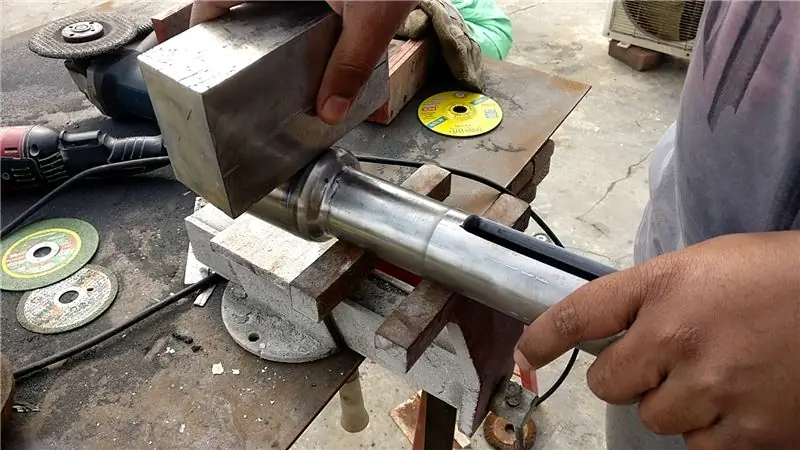
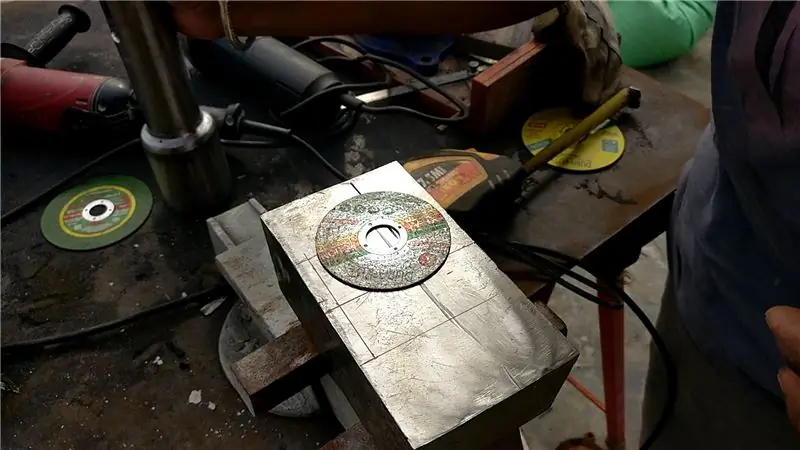
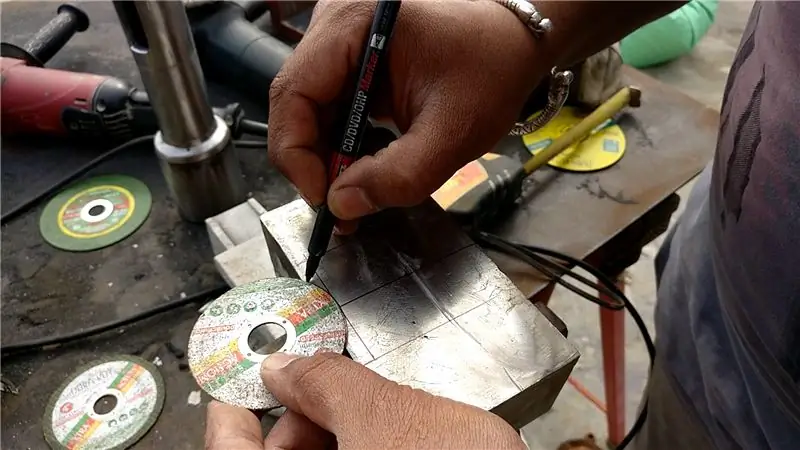
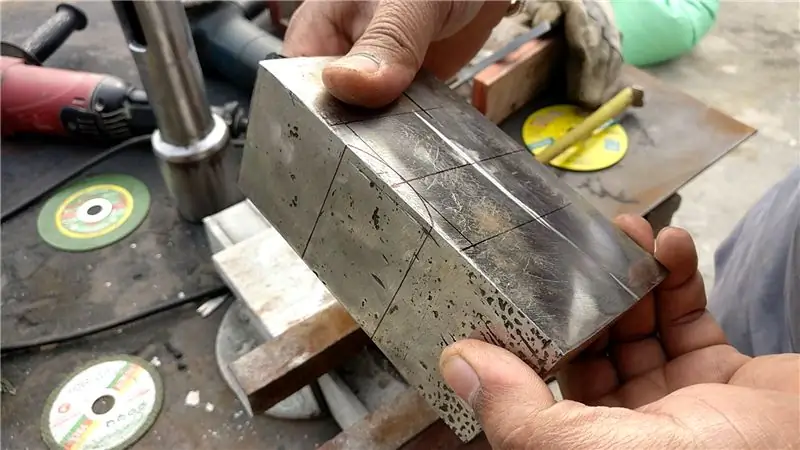
Чтобы соединить стальной блок и ствол вместе, это можно сделать двумя способами. Первый - сделать поверхность ствола плоской путем шлифования, чтобы две плоские поверхности можно было легко сварить. Второй - сделать изгиб на стальном блоке, а затем приварить к нему ствол. Я иду со вторым. Сначала я отмечаю центр на стальном блоке, затем получаю отрезок диска, равный диаметру ствола. Я выбираю эту деталь, чтобы перенести изгиб ствола на блок. Затем я с помощью квадрата прослеживаю их кривую и переношу на другую сторону стального блока. Затем с помощью отрезных дисков болгарки и отрезного круга удаляю этот участок. Во время этой работы я неоднократно проверял, чтобы контур соответствовал точной кривизне для лучшего соединения. Как только я подойду ближе. К этой кривизне с помощью напильников я сделал ее плоской. Я также снимаю фаски с краев, чтобы можно было обработать сварной материал для лучшего соединения. Затем я поставил ствол на место, а затем поместил на него стальной блок, убедившись, что он правильно выровнен. Затем я сделал прихваточный шов, вынул челюсть из зоны удержания и закончил сварные швы. Ток установлен на 150 ампер, что мне кажется меньше, но в итоге работает фантастически. Затем стыки довожу до шлифовки.
Шаг 8: Создание нижней челюсти
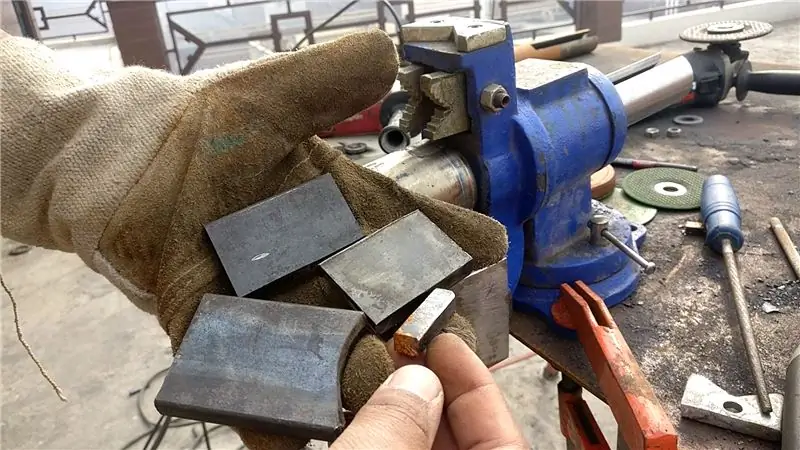
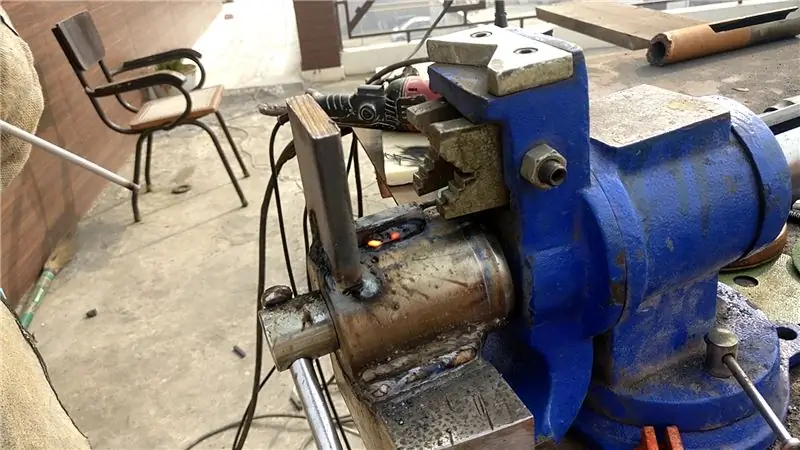
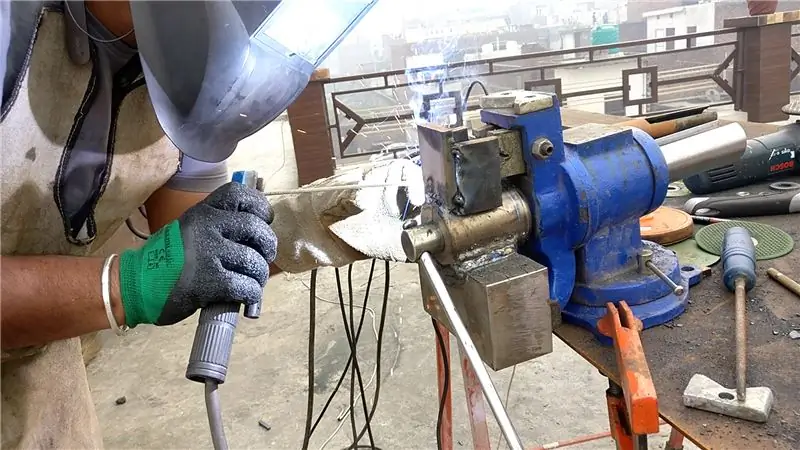
Для создания нижней челюсти я использую стержень из мягкой стали толщиной 10 мм и шириной 2 дюйма. Нижняя челюсть идентична предыдущей. Для этого я вырезал несколько частей, измерив стороны задней челюсти, а затем начал сваривать эти части, создав коробчатую форму, один конец которой открыт для этой вставки. Вверху я приварил небольшую деталь, которая будет выступать в качестве основы для верхней вставки, которую вы увидите на этапе сборки. После этого убираю лишний материал и разглаживаю.
Шаг 9: Профилирование верхней челюсти

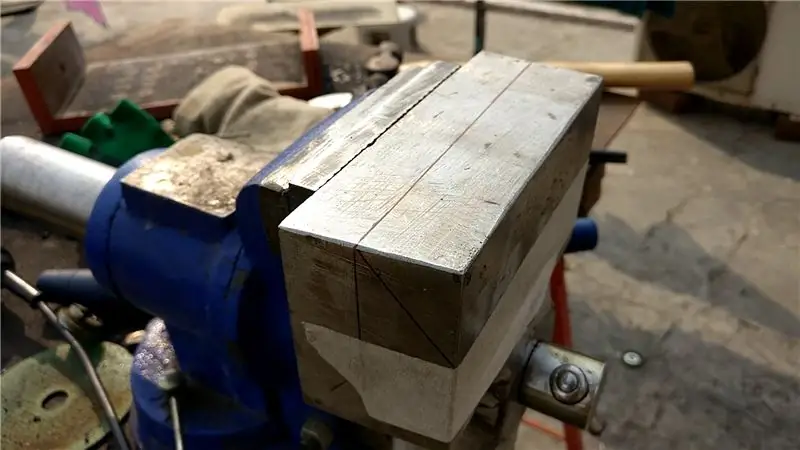
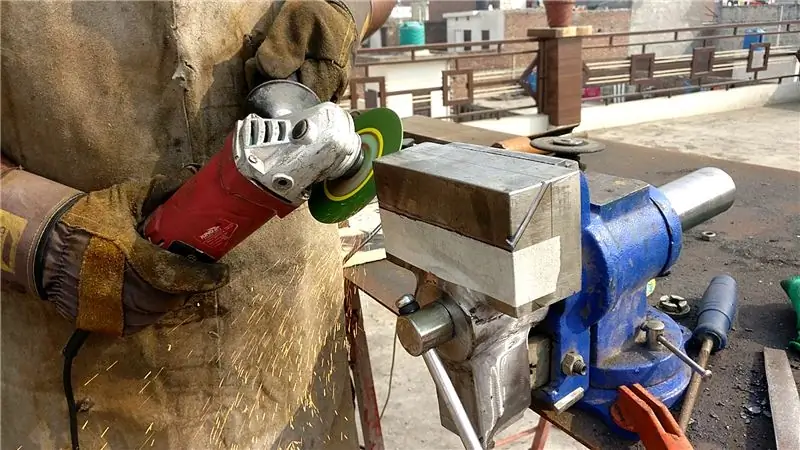
После сварки верхняя челюсть мне кажется довольно громоздкой. Перед сваркой я думал, что могу использовать это в качестве наковальни, но затем я заметил, что такая большая толщина ограничивает работу по заполнению. Поэтому я решил удалить часть материала. Это также уменьшит передний правый. Я сделал несколько надрезов, затем удалил их по частям, а затем разгладил поверхность с помощью лепесткового диска и других шлифовальных кругов.
Шаг 10: закаленные вставки для губок
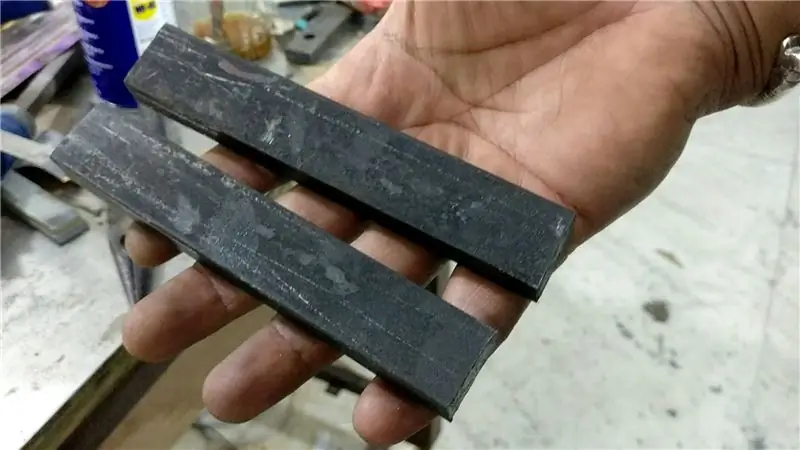
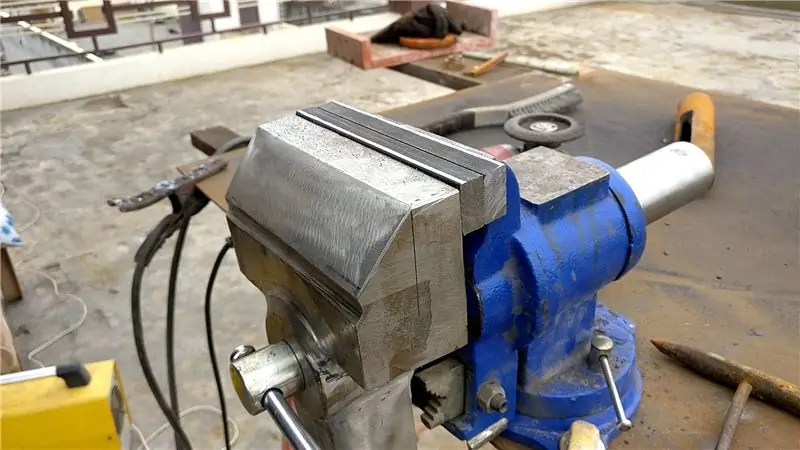
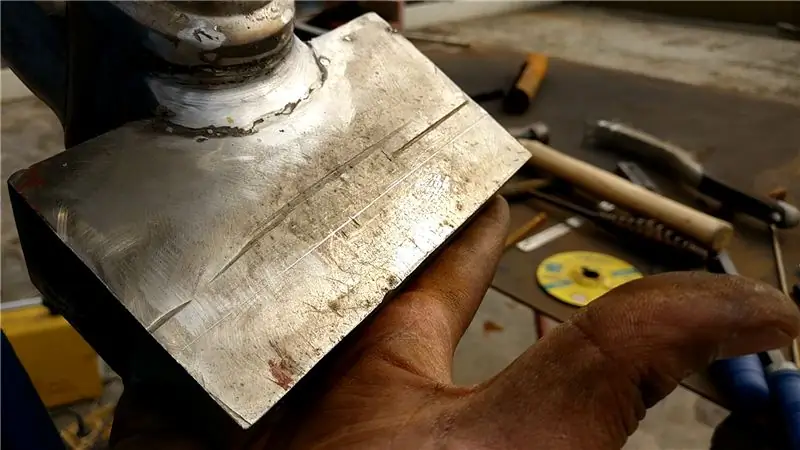
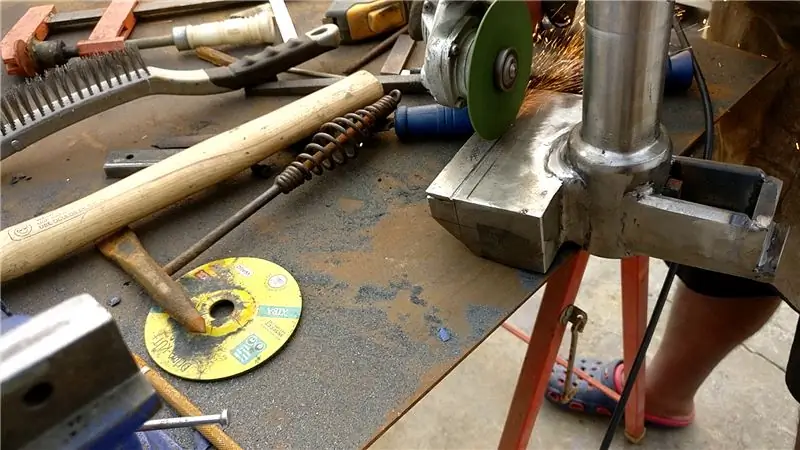
Для изготовления закаленных губок я использую высокоуглеродистую сталь 1095. Отрезаю сталь до необходимой длины. Я сделал это немного больше, чем приклад, идущий с тисками. Они на 1½ дюйма больше оригинала. Один раз я их срезал и держал в тисках. Позже с помощью напильника сделал их плоскими. У предыдущей челюсти есть седло, чтобы удерживать закаленную челюсть, поэтому я делаю то же самое, рисую линию, а затем режу ее с помощью шлифовального станка. Напильник с квадратным напильником приблизит посадочное место к разметке, необходимой для конструкции. Чтобы сделать зазубрины на челюсти для захвата, я сделал отметки с помощью отрезного круга, а затем настроил их квадратным напильником. Эта штука приводит к острым концам этих зубцов. Затем я отмечаю расположение отверстия, а затем просверливаю отверстие и контротверстие, чтобы скрыть винт. Затем я переношу эти места на дрель и также постукиваю по ним. Затем я закалил челюсти, погрузив их в воду.
Шаг 11: Установка аксессуаров
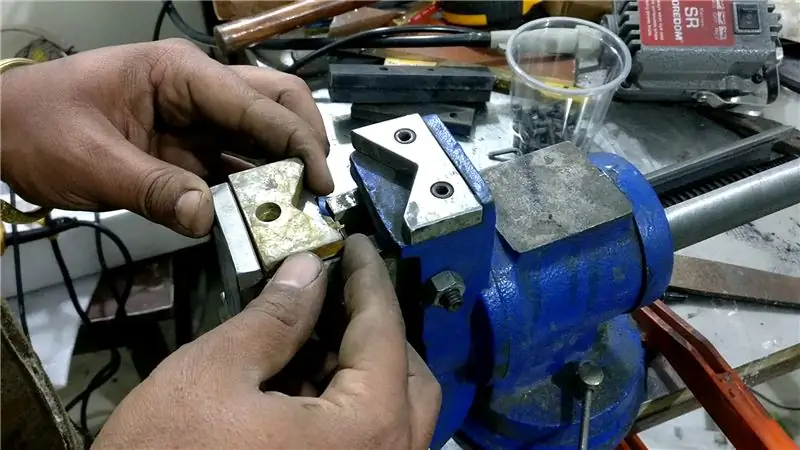
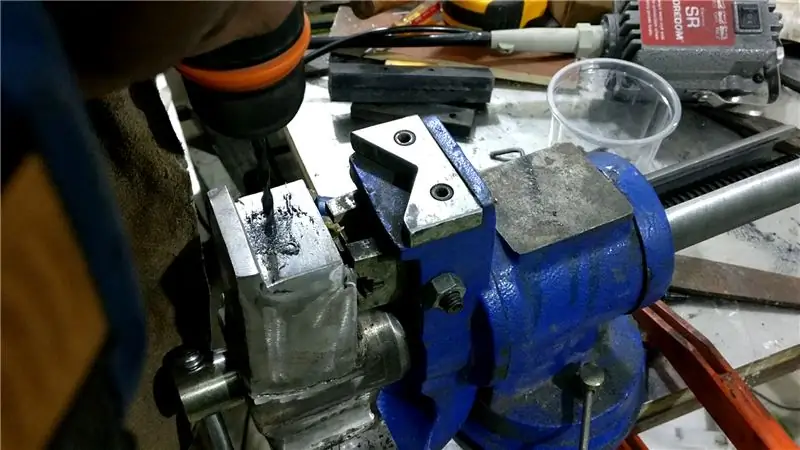
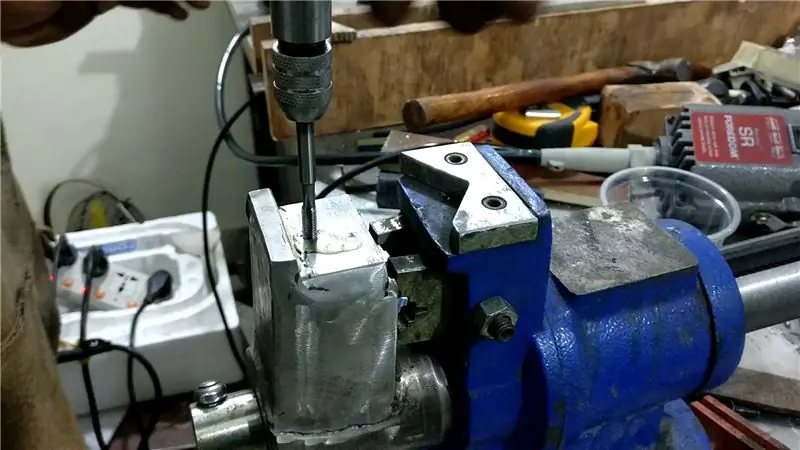
Чтобы установить аксессуары, я помещаю челюсть в верхнюю часть нижней челюсти, а затем переношу место отверстия, просверливаю и ударяю по ним. Чтобы удерживать губку на своем месте, я просверливаю и нарезаю отверстия с обеих сторон, а затем вставляю губку в эту полость и затягиваю винты.
Шаг 12: покраска
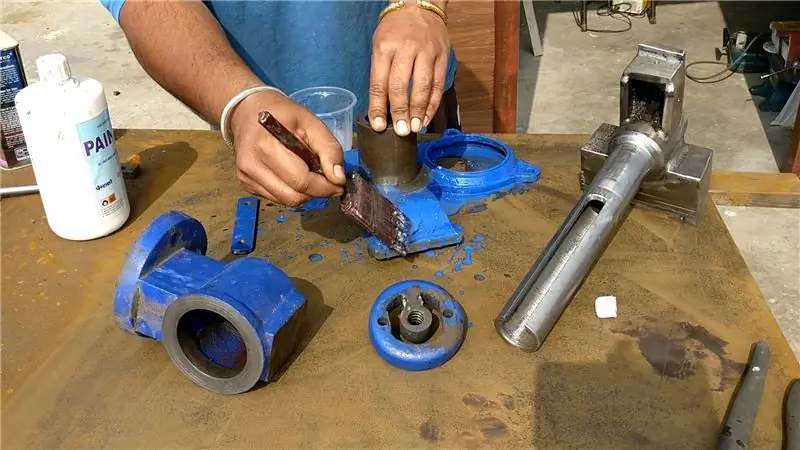
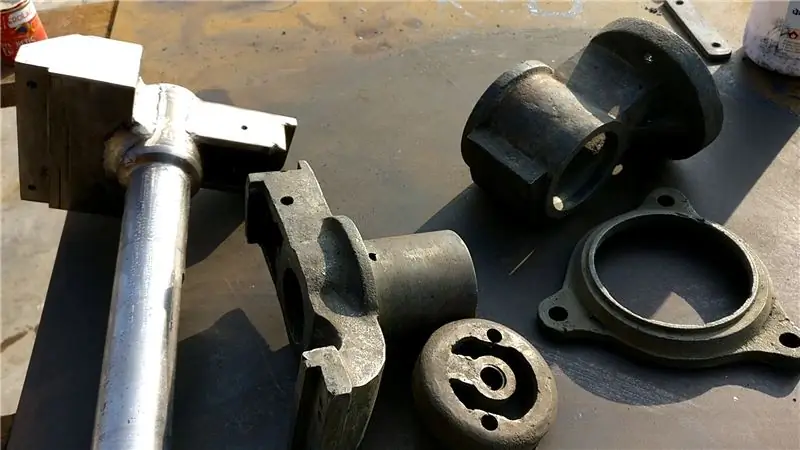
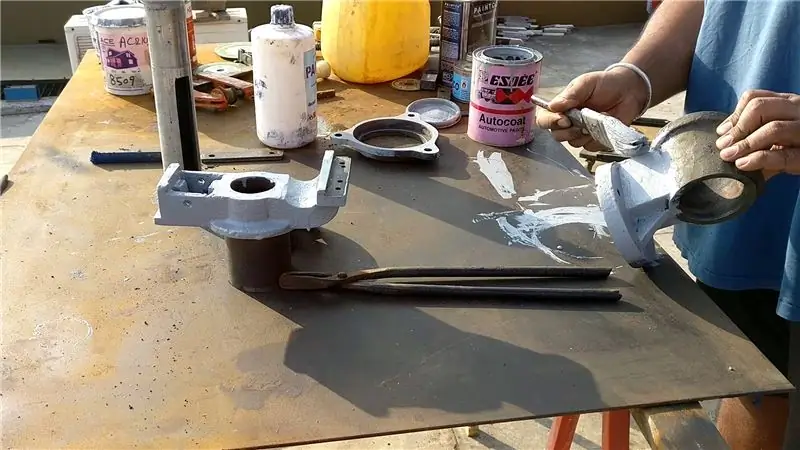
Для окраски я сначала удаляю краску смывкой, а затем наношу на поверхность два слоя серой грунтовки. После этого наношу черную краску на все части тисков. Я нарисовал черную краску, потому что перламутровая краска, которую я собираюсь нанести, нуждается в какой-то темной основе. Но оба типа совершенно разные, потому что один - это основа Оли, а другой - более тонкая. Вот почему на поверхности появляется эффект морщинистости, которая выглядит хорошо. Затем я собираю все детали и определенно вздыхаю с облегчением, потому что я определенно экономлю часть своих денег.
Шаг 13: восхищайтесь работой
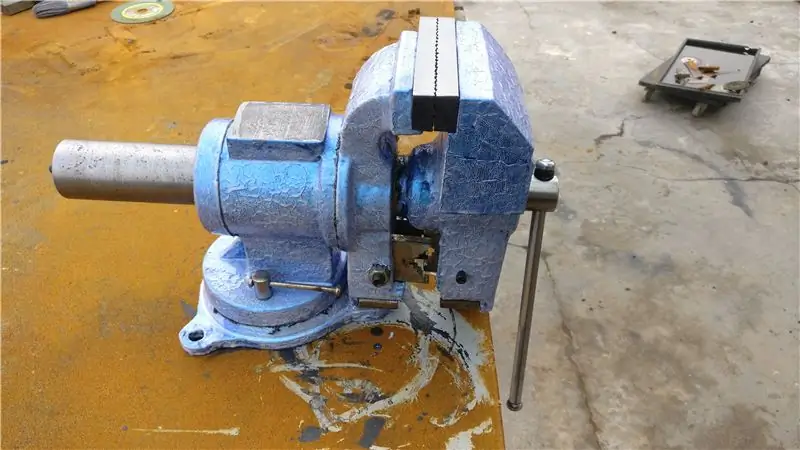
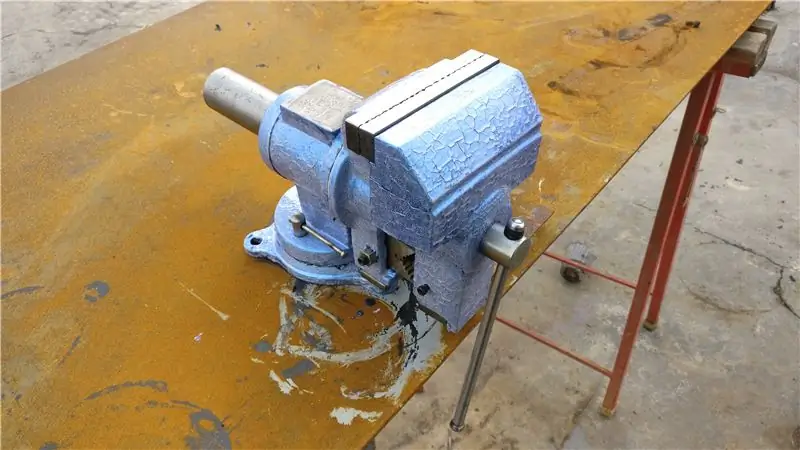
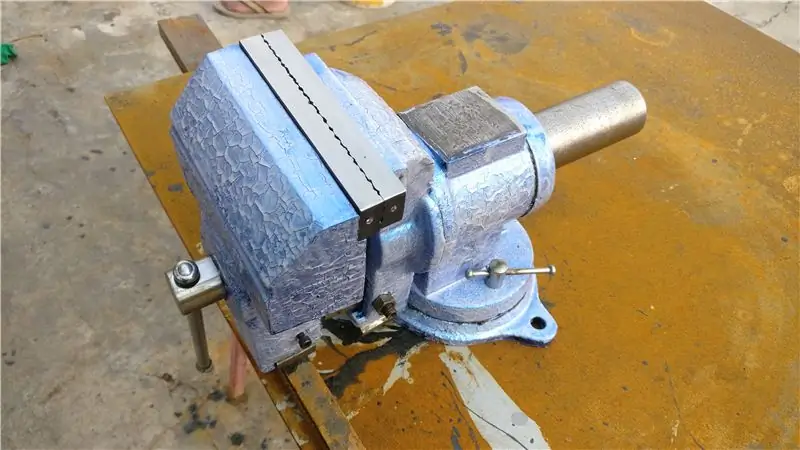
Если вам нравится и у вас есть предложения, обязательно оставьте свои комментарии ниже.