Еще в мае капитан морской пехоты Уильям Махони был вынужден совершить впечатляющую аварийную посадку реактивного самолета AV-8B Harrier на палубу авианосца USS Bataan из-за того, что его переднее шасси не сработало. На видео ниже вы увидите, как Махони совершает идеальную вертикальную посадку самолета без переднего колеса на обычную табуретку. О чем, возможно, не знали многие из тех, кто смотрел видео, так это о последующем ремонте Harrier с помощью 3D-печати после жесткой посадки.
Чтобы как можно быстрее отремонтировать реактивный самолет и вернуть его в состав флота, технические специалисты Bataan и дизайнеры Восточного центра готовности флота (FRCE) на авиабазе морской пехоты в Черри-Пойнт, Северная Каролина, напечатали на 3D-принтере. специальные инструменты для формовки, помогающие заменить поврежденную часть форсунки. Во-первых, аэрокосмический инженер FRCE Дуг Гринвуд работал с командой на борту Bataan, чтобы снять носовой обтекатель Harrier, чтобы оценить ситуацию внутри. Гринвуд объясняет: «Жесткая посадка повредила часть одной из структурных рам в носовом обтекателе».
Команда отметила, что только одна часть рамы самолета была значительно повреждена, и поэтому приступила к замене этой части запасной рамой от FRCE. Гринвуд продолжает: «Усиления из листового металла, называемые дублерами, потребуются для соединения донорской секции с неповрежденной частью рамы, которая осталась в самолете. Перед FRCE стояла задача изготовить дублеры усиления и доставить их на корабль для ремонта». Чтобы получить двойники для авианосца, конструкторы FRCE работали с CAD-моделями от производителя оригинального оборудования оригинальной детали. Получив 25 июня 3D-модель от OEM-производителя, компания FRCE смогла разработать новый дизайн инструментов для формовки листового металла. Затем они приступили к 3D-печати деталей для отправки на Батаан.
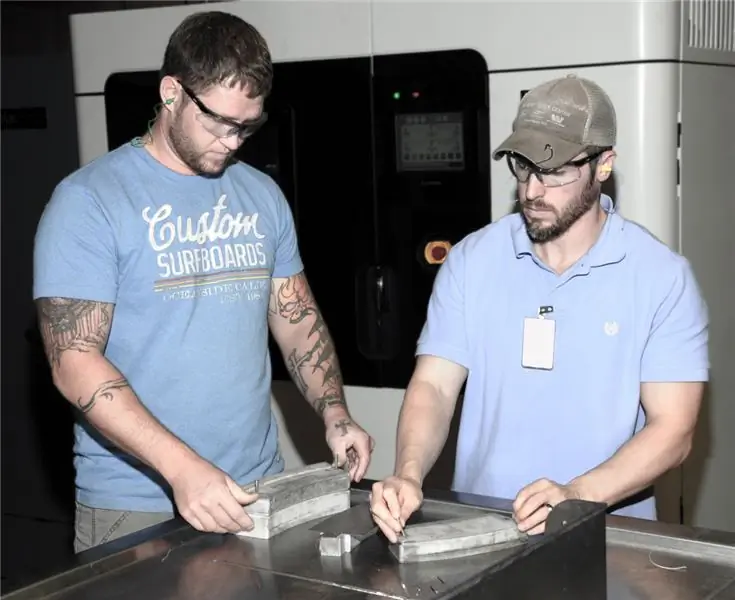
Гринвуд подробно описывает процесс: «Инструменты были изготовлены с использованием поликарбонатного материала, выбранного потому, что он обладает высокой прочностью на сжатие, что позволяет выдерживать давление под высоким давлением до 4000 фунтов на квадратный дюйм (psi). ». 3D-печать формовочных инструментов заняла около пяти часов для одной детали и тридцать для второго комплекта. К 28 июня плоские шаблоны были преобразованы в соответствующие дублирующие детали с использованием этих 3D-печатных инструментов, при этом в процессе формирования осуществлялся контроль качества. После термообработки и окраски новых деталей они были готовы к отправке на Батаан.
Гринвуд объясняет, что без 3D-печати весь процесс занял бы гораздо больше времени: «При использовании традиционных, нецифровых процессов проектирования и сборки инструментов изготовление удвоителей, вероятно, заняло бы две-три недели. Использование трехмерных цифровых данных и AM позволило значительно сократить время и затраты». Он добавляет: «2 июля, через неделю после получения твердотельной модели каркаса, оба комплекта отправились на Батаан для ремонта поврежденного самолета».