В качестве старшего проекта группа студентов-инженеров Университета Аризоны спроектировала, изготовила, собрала и успешно запустила небольшую ракету, используя напечатанные на 3D-принтере детали для нескольких ключевых компонентов.
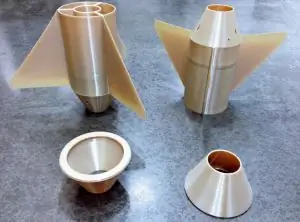
Наставники студентов из аэрокосмического гиганта Raytheon посоветовали им связаться с фирмой по быстрому прототипированию (и недавним приобретением Stratasys) Solid Concepts, которая помогла им с созданием концепции ракеты. С помощью 3D-печати команда создала ускоритель с оперением, всю заднюю часть корпуса, хвостовой обтекатель и несколько корпусов для внутренней электроники. Вот видео сборки и запуска ракеты:
Один из студентов, работавших над проектом, благодарит Solid Concepts и их 3D-печатные детали за то, что они позволили им собрать и запустить ракету в очень сжатые сроки.
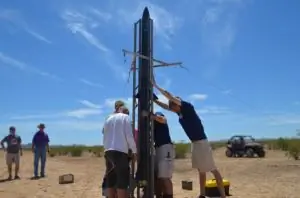
«Одна только конструкция ребра, которая была создана с помощью моделирования методом наплавления (FDM) с использованием высокотемпературного материала Ultem 9085, потребовала бы семь отдельных частей и три дня, чтобы собрать ее, если бы мы построили ее вручную», - с помощь U студента Мэтью Dusard. «Из-за полостей внутри и очень тонких ребер в нашей конструкции 3D-печать была единственным способом создать структуру как единое целое. Мы завернули все напечатанные на 3D-принтере компоненты в углеродное волокно для дополнительной прочности, вставили детали в кормовую часть ракеты и были готовы к работе на следующий день после получения деталей, как раз вовремя для запуска в намеченную дату.”
Ultem 9085 - термостойкая термопластичная нить, подходящая для высокопроизводительных прототипов для транспортной и аэрокосмической промышленности. Этот высокотехнологичный материал для 3D-печати успешно выдержал экстремальную температуру в 1500 градусов при успешном запуске ракеты лишь с небольшим почернением выпускного отверстия и без какой-либо потери структурной целостности. Кроме того, вся конструкция ребра была бы невозможна без 3D-печати, поскольку она была слишком сложной и имела слишком много тонких стенок и открытых полостей, чтобы ее можно было изготовить в виде одной детали. Если бы он был построен с использованием традиционных методов, на его изготовление ушло бы три дня и семь отдельных частей. Команде удалось полностью собрать 3D-печатную конструкцию плавника и подготовить ее к запуску менее чем за день.
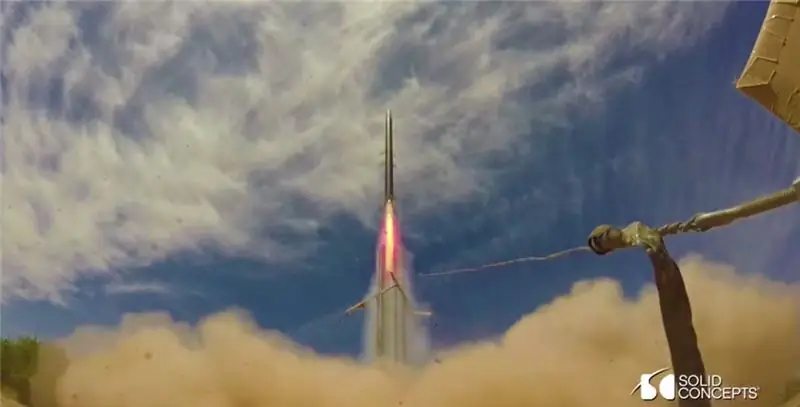
Каждый день мы слышим истории о том, как быстрое прототипирование с помощью 3D-печати используется для вывода продуктов на рынок или резкого сокращения этапа проектирования и прототипирования в цикле разработки нового продукта, но я думаю, что это, вероятно, первая история, с которой я столкнулся, где быстрое прототипирование с помощью 3D-печати помогло группе студентов колледжа получить пятерку за школьный проект.