Кажется, уже давно, хотя только в 2012 году, специализированные веб-сайты по производству велосипедов начали ссылаться на 3D-принтеры, используемые для производства не только прототипов, но и цикла конечного продукта. В то время речь шла об одноразовых велосипедах, изготовленных по индивидуальному заказу. Это еще один признак того, как быстро 3D-печать превращается из возможности в метод производства для очень многих продуктов.
Несмотря на то, что в настоящее время существует ряд существующих циклических проектов, связанных с 3D-печатью, как в промышленном, так и в домашнем хозяйстве, таких как эта инновационная велосипедная рама из углеродного волокна, ускорение промышленных 3D-печатных велосипедов также дошли до финиша.
Renishaw в настоящее время является единственным в Великобритании производителем машин для аддитивного производства, производящих металл. Недавно компания объединилась с Empire Cycles - ведущей британской компанией по проектированию и производству велосипедов, чтобы создать первую в мире серийную металлическую велосипедную раму, напечатанную на 3D-принтере.
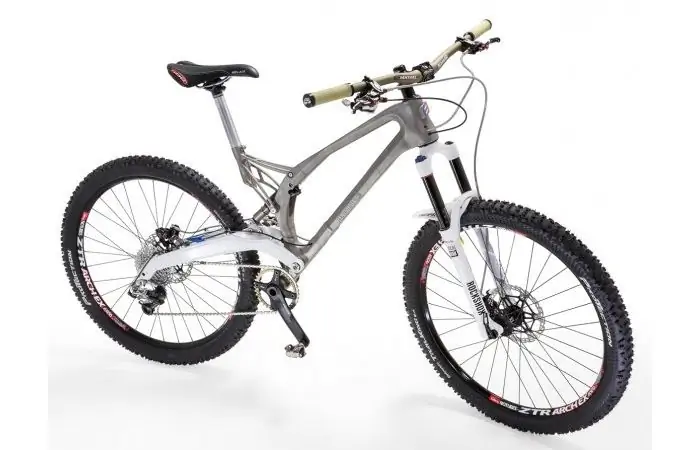
Аддитивная технология от Renishaw позволила Empire создать титановую раму, изготовленную из секций из титанового сплава, а затем склеенных вместе, которая является чрезвычайно прочной и при этом на треть легче, чем оригинал.
Дуэт участвующих компаний перечисляет дополнительные преимущества следующим образом:
Свобода дизайна
Быстрые итерации; гибкость, позволяющая вносить улучшения в конструкцию вплоть до производства
Возможность создания форм, полученных путем топологической оптимизации
Непревзойденная индивидуализация и пошив - изготовление единичных экземпляров так же просто, как серийное производство
Строительство:
Сложная форма с элементами внутреннего усиления
Полые конструкции
Встроенные функции, такие как имя водителя
Производительность, титановый сплав
Кронштейн подседельного штыря на 44 % легче версии из алюминиевого сплава
Чрезвычайно прочный – протестировано в соответствии с EN 14766
Стойкий к коррозии и долговечный.
Строительство двухколесного транспорта уже подготовило для нетерпеливого читателя несколько других захватывающих инженерных примеров, таких как: супербайк energica с использованием селективного лазерного спекания (SLS) в материале Windform на основе полиамида; титановые детали для мотоциклов с помощью прямого лазерного спекания металлов (DMLS) с использованием EOS M270; и изготовленные на заказ детали для мотоциклов с использованием производственной системы Stratasys Fortus 400mc.