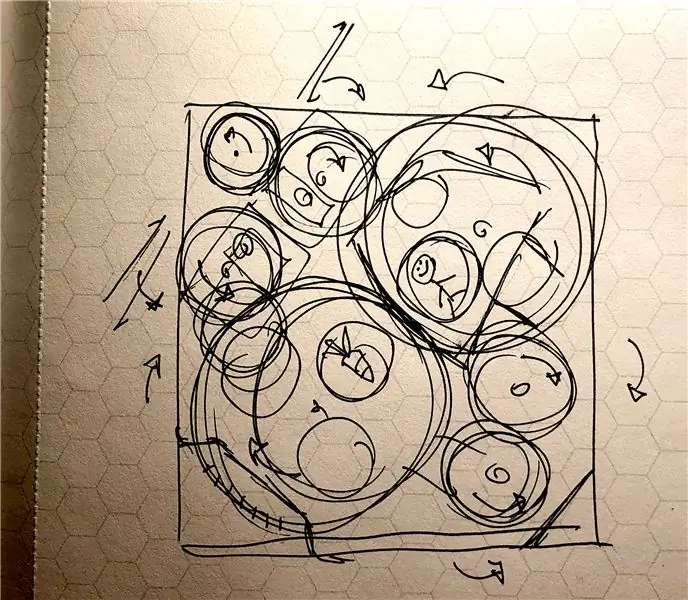
История: Пожалуйста, если вас не интересует история, стоящая за этой штукой, смело переходите к шагу 1 ниже.
Несколько лет назад (2015 г.), в восторге от того, что у нас родился наш первый и единственный ребенок, Анахита, я решила сделать что-то особенное, чтобы отпраздновать это событие и объявить эту новость друзьям и семье. Как художник, изобретатель и инженер, я хотел сделать что-то новое и новаторское, что-то, что я мог бы показать ей, когда она вырастет, и рассказать ей, как много она для нас значила! У нас также были друзья и семья на 5 континентах, поэтому нам пришлось:
- Выдерживать испытание временем. (Чтобы она увидела это, когда вырастет!)
- Должен быть маленьким и достаточно плоским, чтобы поместиться в стандартные почтовые конверты.
- Его необходимо было разместить, не вызывая срабатывания охранной сигнализации на каждой конвейерной ленте!
- Он должен был быть достаточно прочным, чтобы выдержать нагрузку при межконтинентальном почтовом путешествии.
- Я хотел, чтобы она была уникальной, а не поздравительной открыткой, которую можно купить в любом продуктовом магазине.
- Я хотел, чтобы он был интерактивным (имел какой-то пользовательский ввод)
- Я хотел рассказать какую-то историю
- Строительство должно было быть дешевым, поскольку в то время у меня были проблемы (в финансовом отношении)!
В то время я был в Париже, ожидая, пока мои документы полетят в Сент-Луис и присоединятся к моей беременной жене! находясь там, я участвовал в хакатоне и выиграл инкубационный призовой пакет, который включал двухмесячное членство в крутом Maker-Space под названием Usine IO (IO Factory), который был для меня действительно похож на фабрику конфет! со всеми видами производственного оборудования, доступного членам! Я бы остался в Париже максимум на пару недель! так что надо было сразу начать! Я решил воспользоваться своей первой идеей и сделать механическую карту с пользовательским вводом, которая поместится в конверт и будет служить вечно!
В итоге получился очень крутой и прекрасный проект, именно то, что мне было нужно в трудные времена, когда я оказался в Париже, вдали от моей семьи и имел дело с глупой бюрократией! стабильная, поделюсь с другими! поэтому я задокументировал все шаги, сделал фотографии и видео, и, когда, наконец, уезжал из страны, аккуратно положил жесткий диск со всеми документами в рюкзак и прыгнул в самолет, … позже, когда я попытался начать писать историю и создание, жесткий диск не работал! он говорил, что он не отформатирован и издавал забавный шум! все очень печальные признаки испорченного жесткого диска!
Короче говоря, я потерял тонну фотографий, видео, документов и воспоминаний (не только этот проект, но и запечатлел моменты хороших и плохих времен за последние пару лет!). делились в социальных сетях или были созданы резервные копии в облаке, что было только последней частью проекта!
И вот оно! Здесь я попытаюсь воссоздать постройку из того, что осталось за десять тысяч миль пути этого проекта! Я постараюсь воссоздать кое-что из того, что могу, а в остальном я сделаю все возможное, чтобы объяснить процесс.
Шаг 1. Набросок
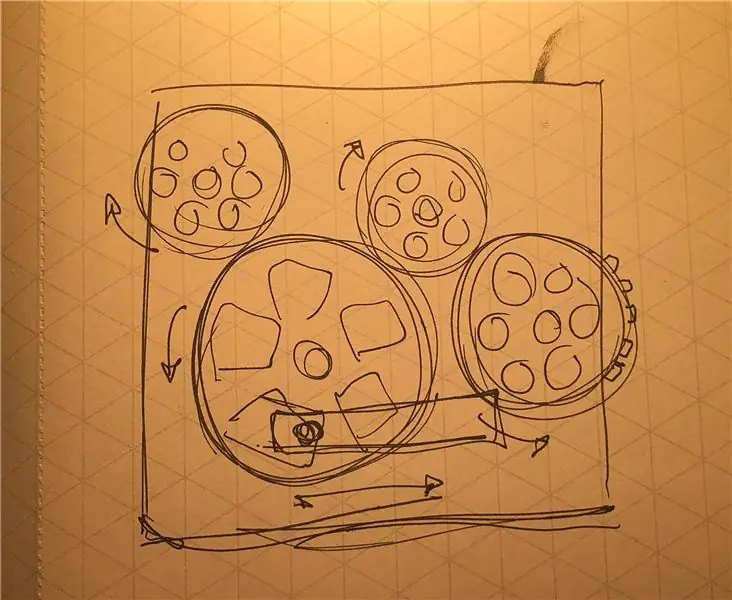
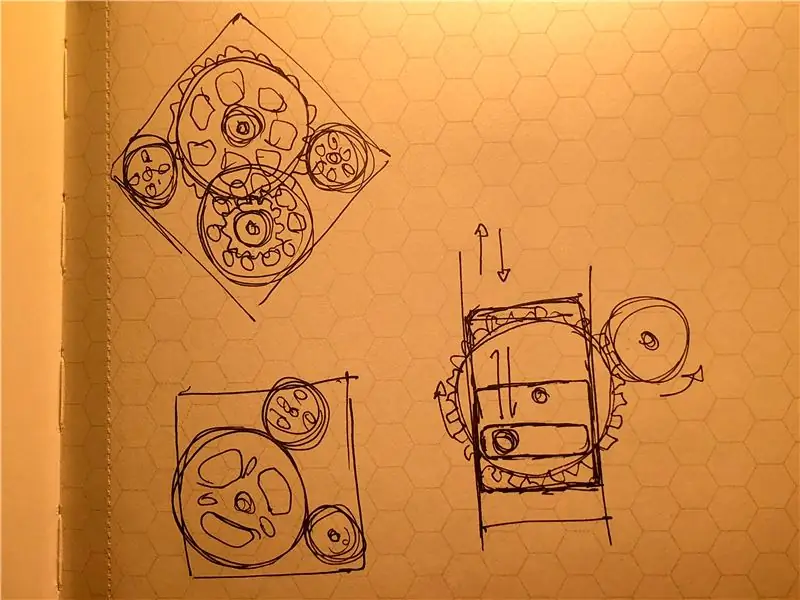
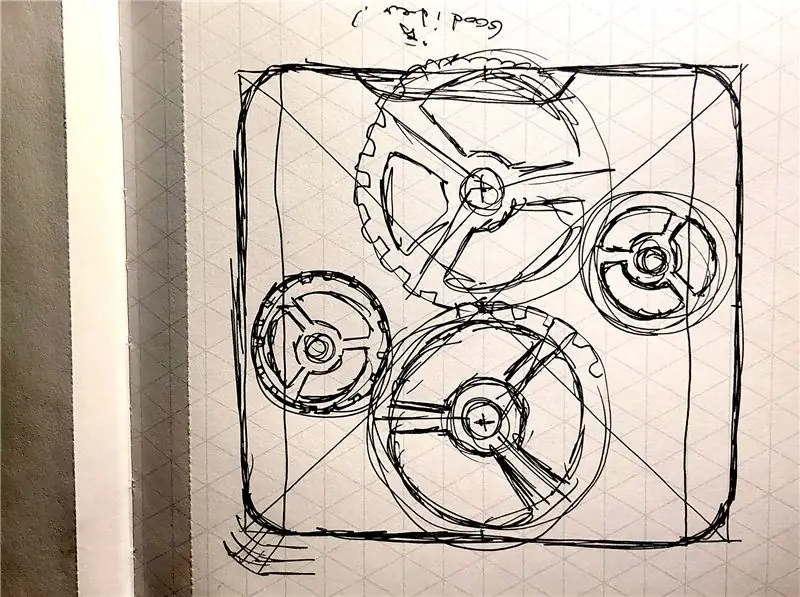
У меня в голове было в целом визуальное представление о том, что я хочу сделать, но из-за ограниченности времени и денег мне пришлось найти способы сначала заставить это работать и быстро, а затем сделать это дешево, чтобы построить!
Дело в том, что воображение дешево и быстро, но не повторяется! Это означает, что вы не можете построить версию 2.0 в своем воображении, основываясь на ее версии 1.0, которая все еще находится в вашем воображении! у вашего мозга нет фиксированной версии, снимка версии 1.0, чтобы проанализировать ее и основать на ней следующую версию.
Простое и быстрое решение - набросать его! Когда вы бросаете это на бумагу, ваш мозг начинает придумывать что-то, основываясь на виртуальном представлении реального объекта, который когда-то был самим воображением.
Итак, вы рисуете свою первую идею, затем смотрите на нее, думая о том, как ее можно изготовить, что может пойти не так в этой конструкции, что можно улучшить и какой материал можно использовать для ее создания. вы позволяете своему мозгу поиграть с этими переменными и придумывать следующую версию, а затем делаете то же самое снова и снова. После нескольких итераций дайте ему перерыв и вернитесь к нему через несколько часов или на следующий день. Кроме того, используйте внешние источники вдохновения, посмотрите некоторые другие интересные примеры промышленного дизайна и посмотрите, можно ли / и как вы можете реализовать те же концепции дизайна в своей идее, и посмотрите, как ваш мозг удивляет вас новыми, свежими вещами!
Вот что я сделал. Первый дизайн был довольно скучным, хотя в то время, когда я писал его на бумаге, он выглядел очень захватывающе! Сначала я думал, что могу спроектировать простую зубчатую систему из кусков картона, но после того, как нарисовал ее на бумаге и подумал о ее проблемах, я очень быстро понял, что бумага / картон - неправильный выбор, они могут скользить друг по другу а также очень быстро изнашиваются при трении. Я представил, что они тоже не смогут плавно повернуть. Затем я подумал о дереве и вообразил - как бы мне ни хотелось делать вещи из дерева - он не будет прочным, гибким и достаточно прочным, чтобы выдержать давление путешествия в почтовой системе, но он также может иметь такая же проблема износа и трения, как у картона.
Шаг 2: выбор материала
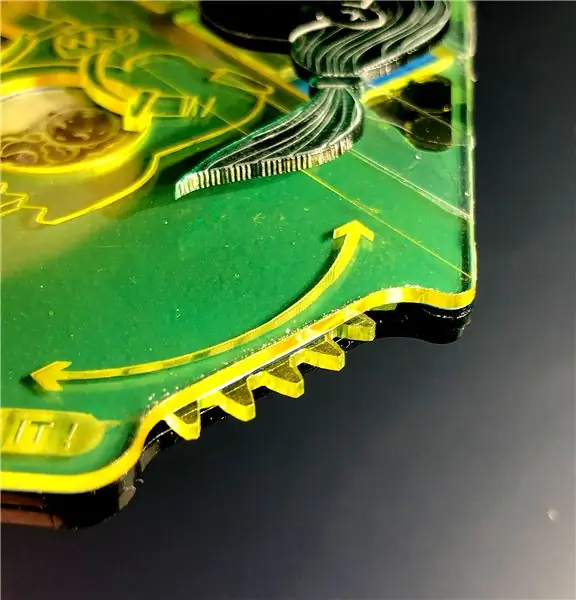
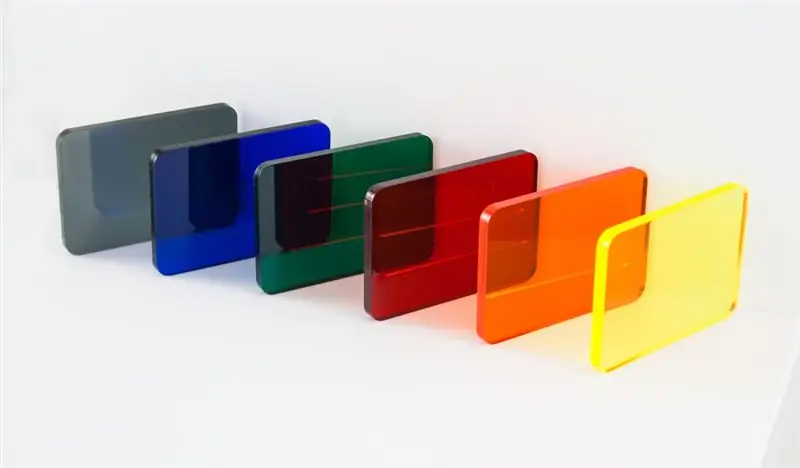
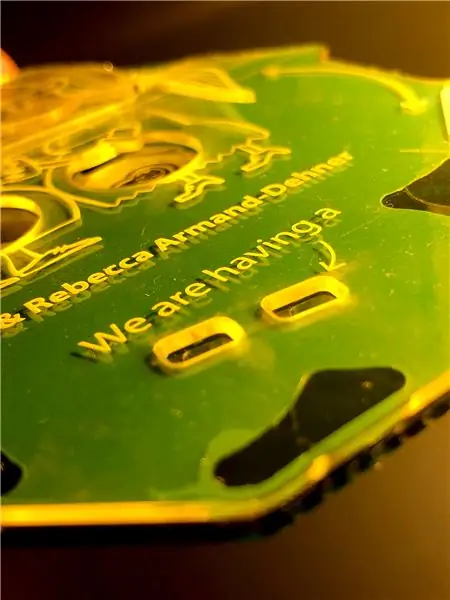
Думая о различных материалах, я склонялся к синтетическим материалам, особенно к стеклоподобным акриловым листам, о которых я знал по некоторым архитектурным проектам, над которыми я работал в прошлом, например, к оргстеклу. Оргстекло - торговая марка компании, продающей их, и вскоре я обнаружил, что мне нужны листы акрила.
Потом я узнал, что есть два вида: экструдированные и литые. каждый со своими особыми характеристиками. Экструдированные листы более дорогие, но они также лучше подходят для лазерной резки, потому что толщина материала более однородна, отлитые листы прочнее и четче (так как при формировании листа меньше напряжения), но толщина может быть более изменчивой и менее точной. Я также обнаружил, что они довольно дорогие! Затем, снова используя свое воображение, я попытался найти способы как-нибудь найти дешевые простыни. После нескольких часов поиска я нашла это место, специализирующееся на продаже объемных акриловых продуктов! Я поехал туда в надежде найти какие-нибудь отрывки, с которыми можно поэкспериментировать, и в итоге они стали моим источником. это было отличное место со всяким акрилом, у них было все! Я также тут же узнал, что существует особый вид клея, который склеивает два листа друг с другом, как всегда было одним целым! так что у меня есть клей и пара разных ломов!
Шаг 3. Преобразование растровых эскизов в векторные
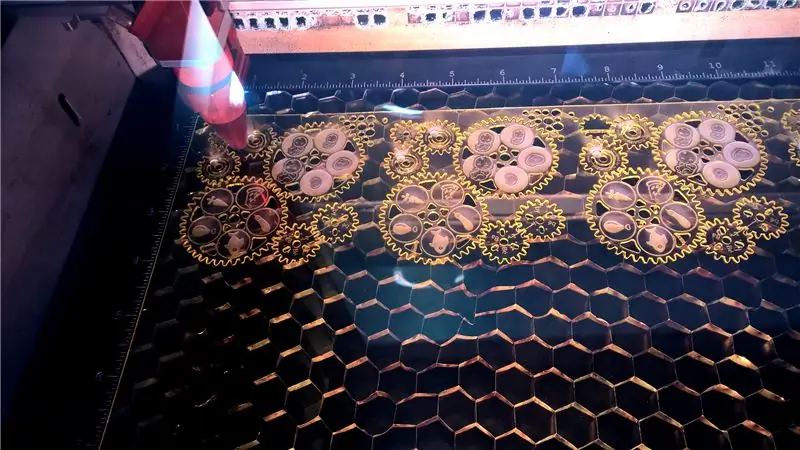
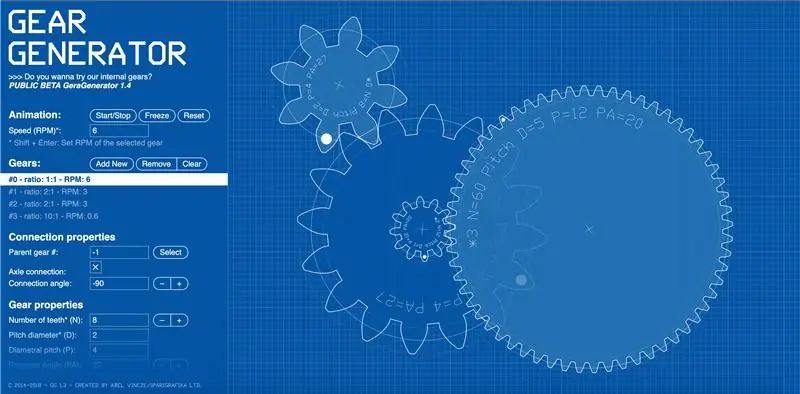
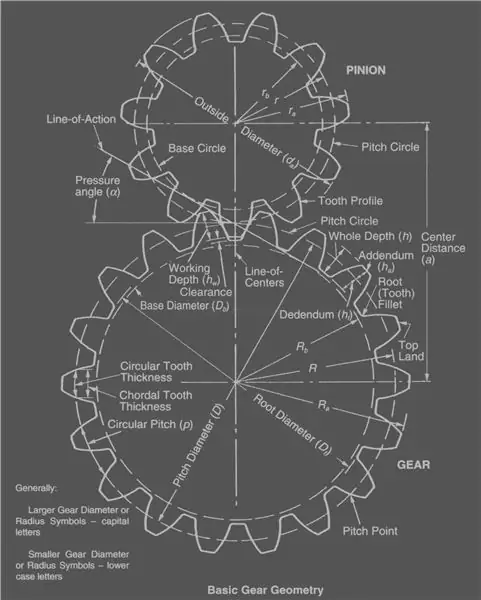
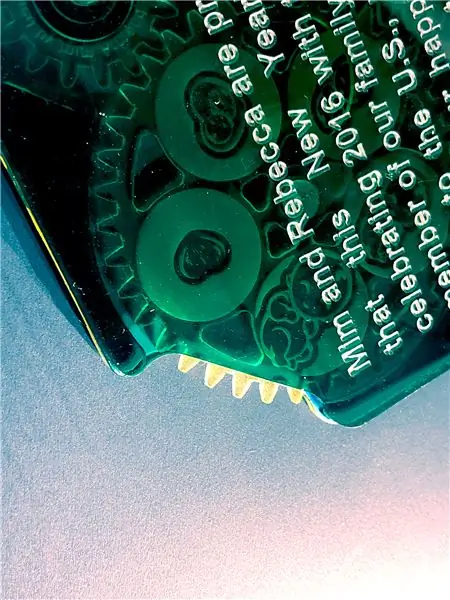
Пришло время поразвлечься с лазерным резаком, но сначала мне пришлось преобразовать свои эскизы в G-коды!
Я никогда раньше не работал с лазерными резаками, я также не проектировал механические шестерни и станки. Однако у меня был большой опыт работы с инструментами и техникой дизайна, как в 3D, так и в 2D, я знаю, как лазерный резак режет технически, и был мастером в использовании инструментов рисования для создания векторных файлов, я знал Adobe Illustrator, Inkscape, и Corel-Draw, наизнанку! Не только как ими пользоваться, но и как заставить их работать! Раньше я разрабатывал плагины для некоторых из этих инструментов!
Так что преобразовать мои наброски в точную векторную графику без потери точности при преобразовании из одного инструмента и формата в другие было проще простого. Были времена, когда некоторые из этих инструментов не играли хорошо с другими, и я просто открывал файл SVG и редактировал некоторые атрибуты вручную, чтобы исправить преобразование (особенно из Illustrator в Inkscape, я помню, была проблема). довольно просто, импортируйте эскиз и используйте его в качестве фонового изображения с уменьшенной прозрачностью, нарисуйте вектор в предпочтительном инструменте (AI в моем случае), затем экспортируйте / конвертируйте в формат Inkscape (который был форматом, принятым с Laser Cutter Machine в Usine-IO), дважды проверьте размеры и цветовые коды и соответствующим образом отрегулируйте / исправьте значения.
Станок для лазерной резки в Usine-IO был действительно хорош, вы могли отправить файл в нескольких цветах и попросить его обрабатывать каждый цвет по-разному, например, красный может означать резку с большей мощностью (сквозной), синий может означать вырезание с более низким цветом (больше похоже на векторное травление для текста или маркировки), а зеленый может означать растровое травление! поэтому идея заключалась в том, чтобы поместить все в один файл и заставить машину проходить дизайн 2 раза, один раз (и первый) для гравировки графики и один раз (и второй) для резки, что было очень важным решением, так как это сделало бы производство Процесс намного проще, поскольку устраняется необходимость повторной юстировки лазерной головки при разных проходах, что приводит к гораздо большей точности в целом.
Gears: Сначала я был напуган физикой и математикой проектирования шестеренок! Поэтому мой первый подход заключался в использовании сторонних инструментов и плагинов для проектирования шестерен с правильным передаточным числом, зубьями и т. д.! но это был кошмар! бесплатные были не такими сложными, как можно было бы надеяться, а коммерческие были либо дорогими, либо были полностью ограничены в пробном режиме. поэтому я провел небольшое исследование, выяснил, что делает шестерни хорошими (угол атаки, количество и толщина зубьев, передаточное число, а что нет) и тбх, не только это было не так сложно, мне это также понравилось Итак, я закончил разработку шестеренок с нуля в Adobe Illustrator, я бы нарисовал круг желаемого размера, разделил его на желаемые сегменты, выдавил / скосил сегменты друг друга и сгладил края, я бы оставил крошечное пространство в мой дизайн, так что зубцы не подходят друг к другу (думал, что это может привести к блокировке системы), и все получилось прекрасно! Я думал, что могу добавить немного смазки, чтобы сделать вещи более гладкими, но даже в этом не было необходимости! Это также дало мне возможность сделать более красивые и легкие шестерни, снизив общий вес и позволив вырезать некоторые другие элементы внутри неиспользуемого пространства больших шестерен. шестерни и движущиеся элементы и механическая физика! большая часть этого материала предназначена для совершенствования вещей, а некоторые из них могут вообще ни на что не повлиять, за исключением удовлетворения университетов, которые заплатили Джо за публикацию статьи об этом! Как инсайдер, я могу сказать вам, что значительная часть этих статей может быть совершенно неправильной! и по большей части это нормально и ожидаемо!
TL; DR! В то время не было много бесплатных и хороших инструментов для создания дизайнов шестеренок, однако в настоящее время небольшой поиск в Google даст более многообещающие результаты! например, я нашел этот сайт очень интересным и простым в использовании (https://geargenerator.com), попробуйте!.. есть также другие, просто Google, или DuckDuckGo, или что-то еще!
Шаг 4: Метод проб и ошибок лазерной резки
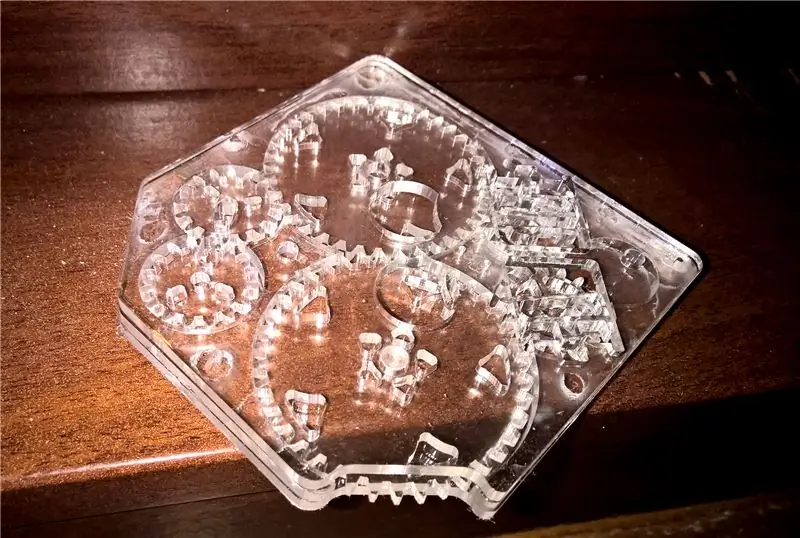
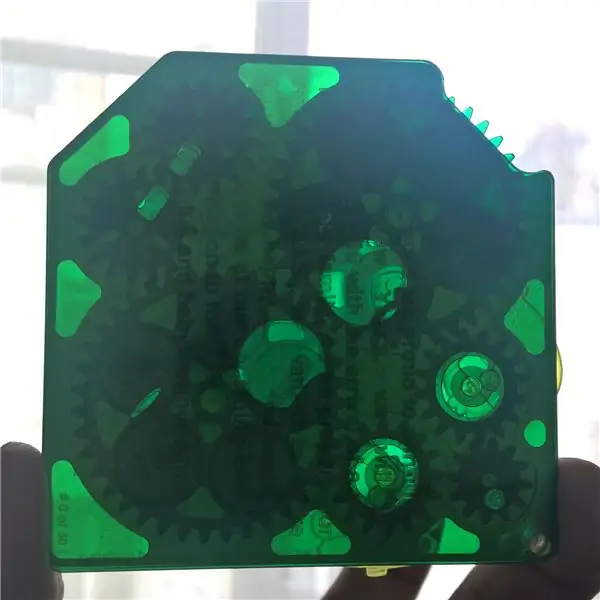
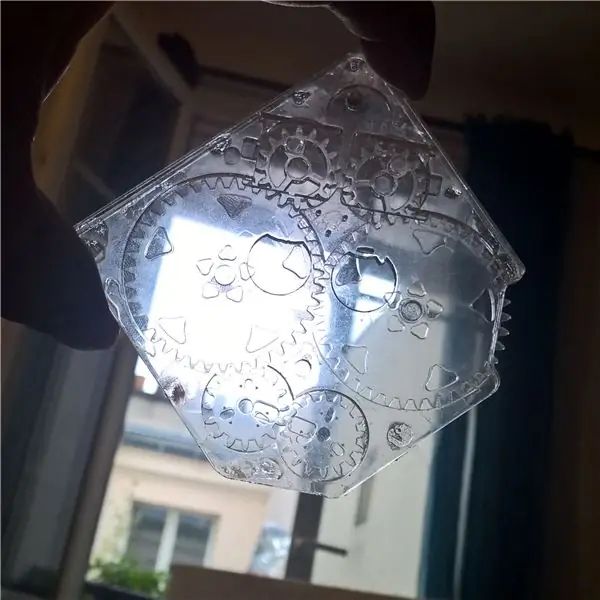
В то время у Usine было четыре станка для лазерной резки, два больших и два поменьше. Оказалось, что эти станки очень популярны и очень часто заказываются! это оказалось проблемой, каждая из этих машин имеет разный уровень точности, мощности и калибровки, и необходимость переключения между ними делает детали, несовместимые друг с другом. Также в зависимости от времени суток настройки должны были быть разными! То, что сделало бы чистый срез на первой партии в 8 часов утра, обожгло бы края к 16 часам!
Другой большой проблемой, на решение которой потребовалось больше всего времени, была корректировка конструкции с учетом особенностей и характеристик лазера. Как я уже сказал, это был мой первый опыт работы с Laser, и вскоре я узнал, что лазеры чрезвычайно хороши для выполнения определенных разрезов и конструкций, но они борются с некоторыми другими. Например, это было бы намного проще, потребовало бы гораздо меньше времени и создания гораздо меньше. вибрация, чтобы лазерная головка следовала изогнутому углу по сравнению с острым углом, хотя эта кривизна добавляет вычислительной сложности конструкции. Кроме того, я узнал, что в целом ошибки калибровки становятся более выраженными по мере удаления головки от нулевое происхождение, поэтому, независимо от того, насколько малы погрешности машины, всегда стоит, когда голова находится дальше всего от нулевого основания, а также, если вы получаете странные формы, такие как слегка эллиптический круг или если начало и конец замкнутого пути встречаются, прежде чем что-либо еще, проверьте, достаточно ли хорошо ваша среда прикреплена к основанию (обычно соту или металлической решетке), я использовал небольшие магниты и металлические грузы, чтобы предотвратить перемещение среды, когда мощный лазер голова делает быстрые движения по машине (все трясет!)
Еще один совет - подумайте о движении головы при разработке траектории, для меня это сэкономило много времени и сделало разрезы более точными. Дело в том, что, в зависимости от материала, тепло, выделяемое лазером, может заставить материал немного расширяться, сжиматься, деформироваться или изгибаться, а если у вас много проходов в одной и той же области, это может сделать эффект более драматичным. Помня об этом при рисовании линий, сделайте более чистый и точный разрез. Это также помогает машине лучше справляться с дымом и испарениями (распределяя количество дыма в заданное время), опять же, в результате получаются более чистые и стабильные разрезы, а также уменьшается количество ожогов и повреждений зеркал. Простое решение этой проблемы - использовать в дизайне несколько цветов обводки, каждый для одного прохода головы, и назначить всем им одинаковую мощность, скорость и параметры резки (только для того, чтобы заставить голову сначала обрезать цвет, затем следующий и так далее, чтобы распределить и рассеять тепло). поверьте, это очень помогает!
Есть и другие разумные дизайнерские решения, которые вам, возможно, придется принять, зная, как работает лазерный резак, например, если у вас есть несколько вложенных полных разрезов (формы замкнутых контуров друг в друге) материала (что здорово экономит время и материал), вы не можете отправить их все в машину и ожидать, что она пройдет их в правильном порядке. Если машина сначала обрежет внешнюю форму, деталь может упасть в лоток и не оказаться там, когда голова решит начать резку внутренней формы! Опять же, в качестве простого обходного пути сделайте разные цвета обводки и заставьте голову начинать от самых внутренних форм к внешним.
Шаг 5: Совершенствуем концепцию
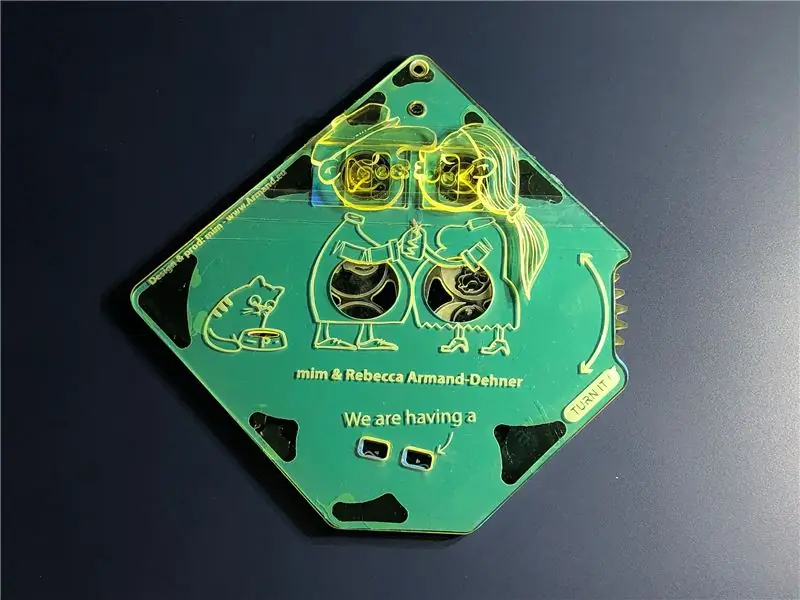
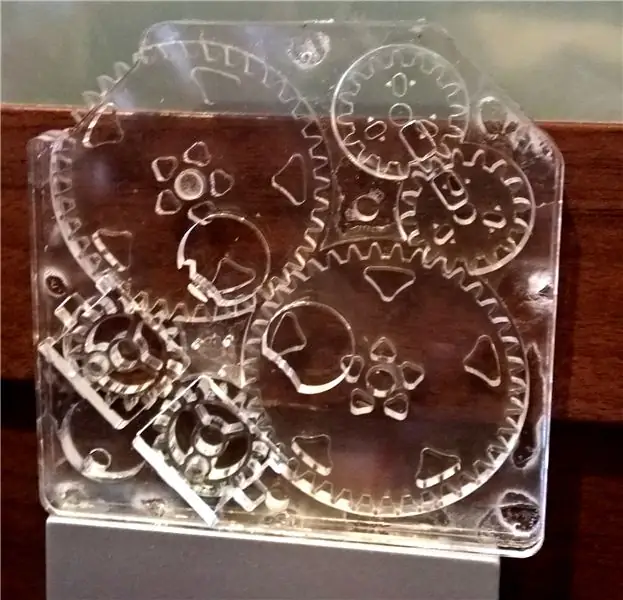
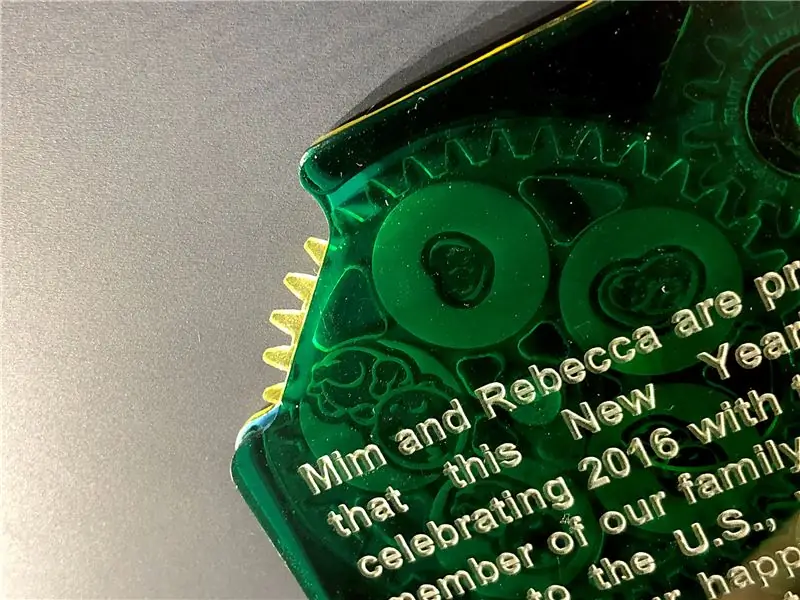
Делаем дизайн проще / минималистичнее:
Как архитектор, я научился любить простоту! Я пробовал разные конструкции с разными принципами механического движения, включая планетарную зубчатую передачу (которую я создал как другой проект для создания визитной карточки ограниченного выпуска!), Я также пробовал разные механизмы передачи круговое движение шестерен до поступательного движения головок. Окончательная конструкция состояла из 7 шестерен, используемых для преобразования движения в разных направлениях, и двух валов с пазами и фрезой, используемых для преобразования кругового движения в возвратно-поступательное. Передаточное число было разработано так, чтобы движение было плавным и удобным. Я также обнажил часть одной из больших шестерен и использовал ее в качестве пользовательского ввода для включения и питания системы.
Уменьшение толщины:
Сначала я использовал акриловый лист толщиной 4 мм для внешних слоев и толщиной 2 мм для внутреннего слоя. Я также протравил и вырезал внешние слои, каждый 1,5 мм, чтобы создать корпус для внутреннего слоя (шестерни), поэтому общая толщина будет 8 мм, но после нескольких экспериментов я решил использовать 2-миллиметровые листы для всего и полностью исключить внутреннюю резьбу, выбрав общую толщину 6 мм. это оказалось очень важным решением в успехе проекта, поскольку оно уменьшило сложность конструкции и производства и сделало конструкцию более устойчивой к ошибкам, сохранив проект, так как после окончательного пакетного вырезания я понял, что были некоторые несоответствие толщины листов, которое могло бы вызвать серьезные проблемы при сборке с предыдущей компоновкой.
Уменьшение слоев:
Все вращающиеся элементы (шестерни) были помещены в один слой, оставался только один небольшой вал, переходящий из одного слоя в другой (для преобразования кругового движения в возвратно-поступательное). если бы толщина не была проблемой, идеальный дизайн должен был бы состоять из 6 слоев. Я удалил половину слоев, встроив их функции в другие слои с двумя компромиссами, первый из которых заключался в том, что на одном из внешних слоев должен был быть движущийся элемент (ни к чему не прикрепленный), который мог бы выпасть! Я исправил эту проблему простым решением: я наклеил прозрачный скотч поверх движущегося элемента, положив еще один слой ленты сбоку и замаскировав только открытые части, которые были обращены к движущейся части (чтобы она не прилипала к движущемуся элементу). Это!). Другая проблема заключалась в том, что головы (которые двигались взад и вперед, целовали друг друга!) оказались без слоя! что на самом деле выглядело довольно круто, что сделало визуальные эффекты более интересными и позволило мне уменьшить общий размер карты (поскольку теперь головы могли выходить за границы карты, когда они были наиболее удалены друг от друга), с компромиссом в том, чтобы сделать эти элементы более подвержены риску поломки во время транспортировки. Мое решение этой проблемы заключалось в том, чтобы прикрепить голову к квадрату с прорезью как самое слабое звено (связанное с очень небольшим количеством клея), чтобы при параллельном напряжении (что маловероятно в конверте) голова отсоединится. от вала, а не сломался, и это действительно сработало, и среди всех доставленных копий был только один случай (насколько мне известно), когда головка не была подключена, и даже в этом случае получатель решил, что они просто нужно приклеить обратно!
В первоначальном дизайне было также два дополнительных слоя толщиной в бумагу, вырезанных из скользких пластиковых листов, чтобы уменьшить трение между слоями (а также для визуальной эстетики), которые были устранены в конечном производстве (по большей части!), Поскольку на самом деле это было не нужно!
Шаг 6: Нарезка последней партии
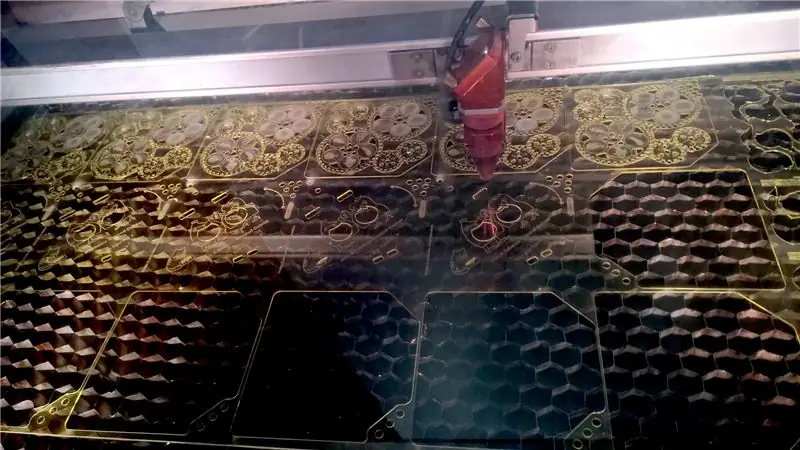
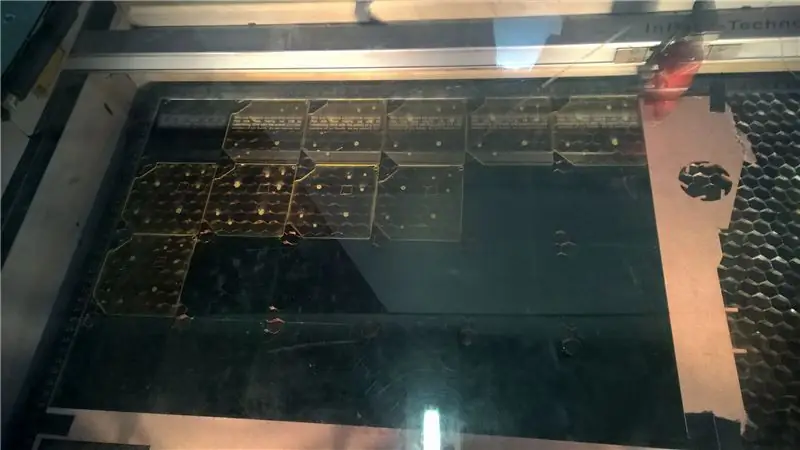

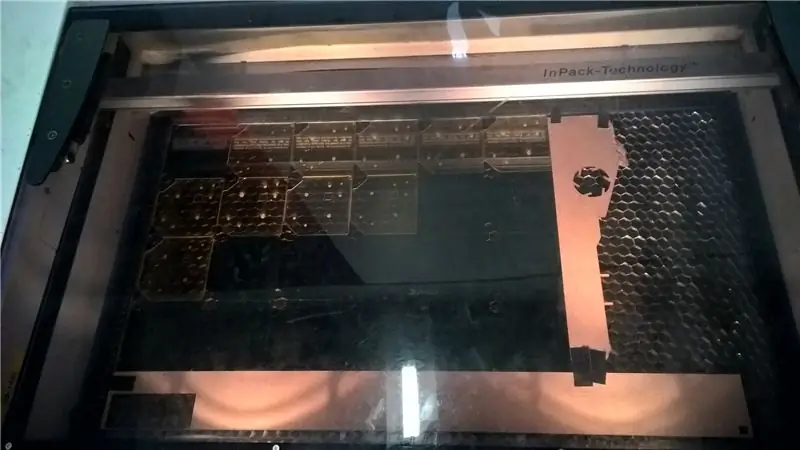
Я трачу 80% времени на подготовку к производству, и это было лучшее, что я мог сделать! из-за этого изготовление и выпуск последней партии доставили удовольствие! Я протестировал и разработал обходные пути для всего, что могло пойти не так или вызвать проблемы во время производства! Единственная проблема заключалась в том, чтобы заказать им машины! которые вам не разрешалось бронировать более 1 часа в день! поэтому я пошел туда рано утром, потому что знал, что никто не придет в Усине-ИО и не закажет машину так рано! Вместо этого я забронировал свое время на 10:30 и надеялся, что никто не решит встать с постели раньше, чтобы прийти и вырезать вещи лазером! и это оказалось правильным, но даже этого времени не хватило, чтобы все вырезать и протравить!
В итоге я потратил 2-3 дня, пытаясь использовать любую минуту, когда машины были доступны для завершения моей работы, самое сложное - это калибровка машин (так как мне пришлось использовать другие), но ко второму дню я придумали способы сделать это очень быстро и эффективно! Я решил хранить детали, вырезанные на разных станках отдельно, хотя, как я подумал (правильно), лазерный луч сам по себе может иметь разные точные размеры на двух станках (из-за различий в калибровке или разных марок / сборки и возможностей труб с разной мощностью), что добавило немного времени и сложности следующему этапу - сборке!
В этой последней партии я использовал только 2-миллиметровые листы двух разных цветов: темный (для внутреннего слоя) и светло-зеленый (для внешних слоев), я также вырезал еще пару листов на случай, если у некоторых из них возникнут проблемы (которые они сделал! как архитектор / инженер вы должны знать, что все, что может пойти не так, пойдет не так!), у меня также были шестерни, помеченные / пронумерованные в моих проектах, чтобы я мог использовать именно ту шестерню, которая была вырезана в ее точном месте, а именно очень помогли заставить вещи работать вместе (помните, в одном из шагов я сказал, что предел погрешности увеличивается по мере того, как лазерная головка удаляется от исходной точки? Если вы используете компоненты, которые были вырезаны близко друг к другу, вы можете работать вокруг этих ошибок, поскольку два компонента, близкие друг к другу, оба будут иметь почти одинаковое количество ошибок, что уменьшает погрешность между ними в разы. С другой стороны, если вы используете 2 компонента из двух противоположные стороны обрезанной среды, там у вас будет наибольшая разница / e ррор)
Шаг 7: Сборка
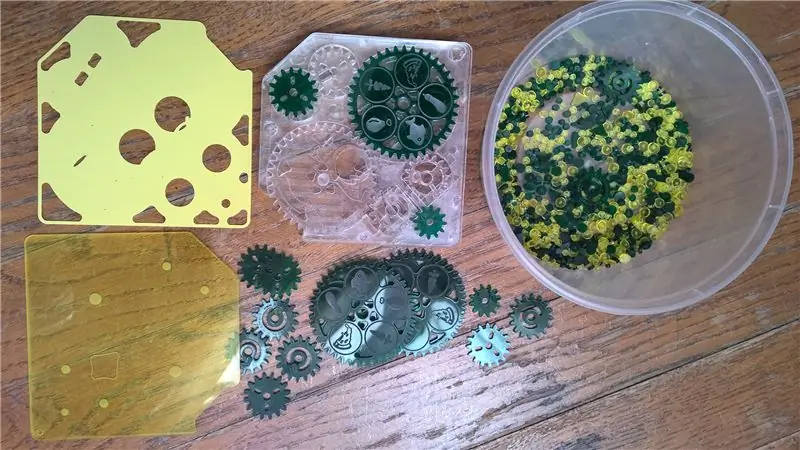
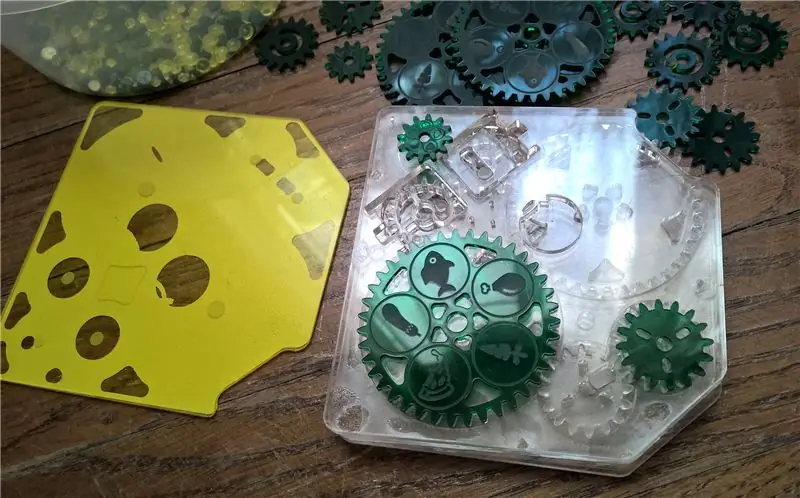
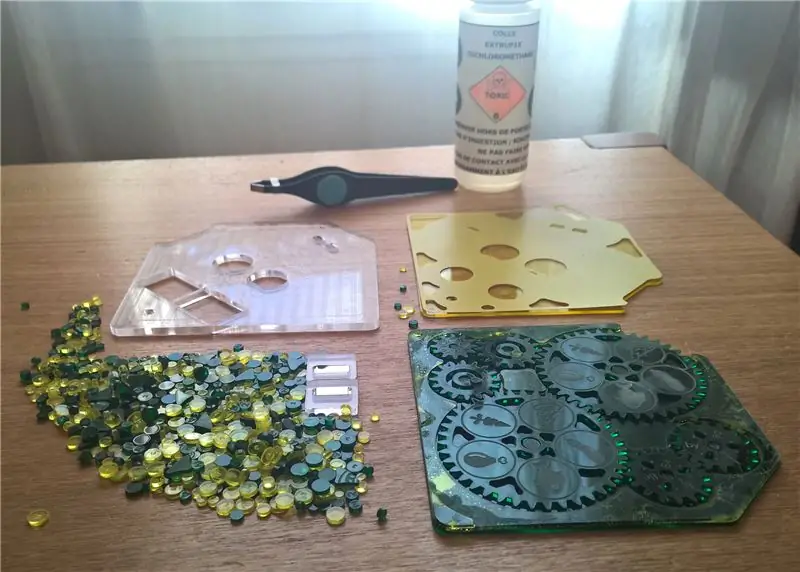
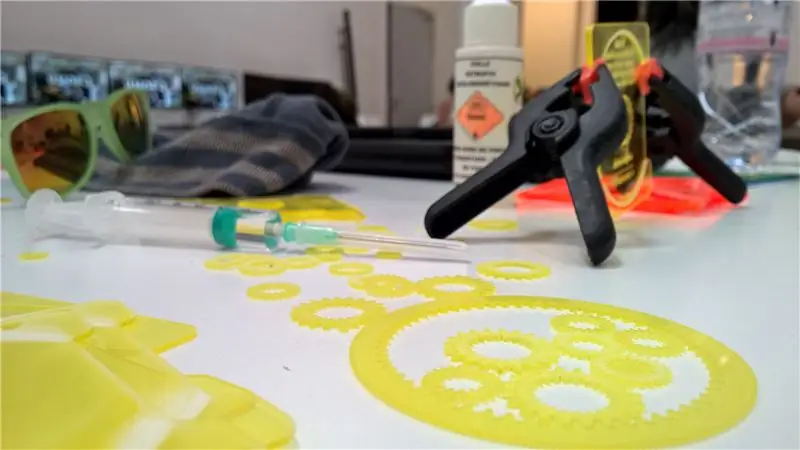
ИМХО, это может быть та часть, которая часто получает меньше всего внимания и вызывает больше всего усилий, затрат и времени при производстве и прототипировании. Я знал, что собрать все будет нелегко, и из-за этого, Я имел в виду этот шаг с самых первых шагов, особенно в процессе проектирования, я думал о сборке и проектировал компоненты таким образом, чтобы я мог делать приспособления для них, чтобы их можно было размещать и собирать быстро и эффективно, но при этом очень точно!
И вот что я сделал! По большей части я использовал неиспользованные части, которые были вырезаны (из шестеренок и других элементов), чтобы сделать приспособления, которые использованные части могли бы легко вставляться, затем я склеивал их и зажимал, перемещал их и начинал со следующего кусок! и это сработало очень хорошо, по большей части, однако мне приходилось создавать дополнительные приспособления для деталей, которые были вырезаны на разных машинах, а иногда и для двух дальних сторон листа для большей машины (из-за допустимой погрешности I говорил о).
В целом это был простой и плавный процесс, он занял меньше дня, и возникла всего пара неожиданных проблем, таких как склейка нескольких деталей, вышедших из строя (потеря шестеренки или что-то еще!) Или падение крошечного количества клея. (случайно) и приводя к блокировке всей карты, потому что одна из шестерен была приклеена на место (в одном случае я пытался продолжать вращать шестерни в надежде, что это помешает клею заблокировать ее! но не только это произошло наконец, но он также нанес крошечное количество клея на всю систему, сделал все непрозрачным и в какой-то момент заблокировал все это!)
Шаг 8: Отправьте их
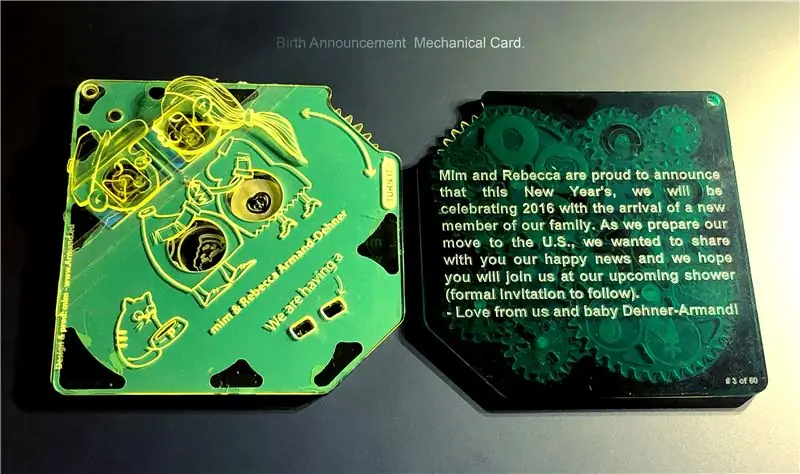
Как я уже сказал, я вырезал еще пару листов, чтобы оставить несколько для себя и раздать позже! Но, конечно же, оказалось, что первоначальный список, который составила моя жена, не был "полным", она решила добавить еще (на 20% больше, если быть точным!), Поэтому я отправил их все, кроме одного *!
Я получил несколько красивых конвертов, вставил их и отправил двумя партиями, все они были доставлены целыми, за исключением нескольких, которые так и не были доставлены (утеряны), и одного, который был доставлен с одной из отклеенных головок (которую получатель легко починил.) Все либо звонили, либо писали в ответ, чтобы рассказать нам, как сильно они их любили, и я действительно гордился своими инженерными навыками в первый раз, впервые создав беспрецедентную вещь! Я думал, может быть, я смогу коммерциализировать это как новый вид поздравительных открыток, но, как и многие другие идеи, это еще нужно сделать, я перешел к другим проектам / идеям и больше не трогал их! Может быть, в какой-то момент я вернусь к этому снова и создам V 2.0!
*Ой! и я забыл упомянуть! Я их пронумеровал! Я выгравировал номер в углу каждой карточки, так что они должны быть довольно коллекционными! а серийный номер №1 я оставил себе!
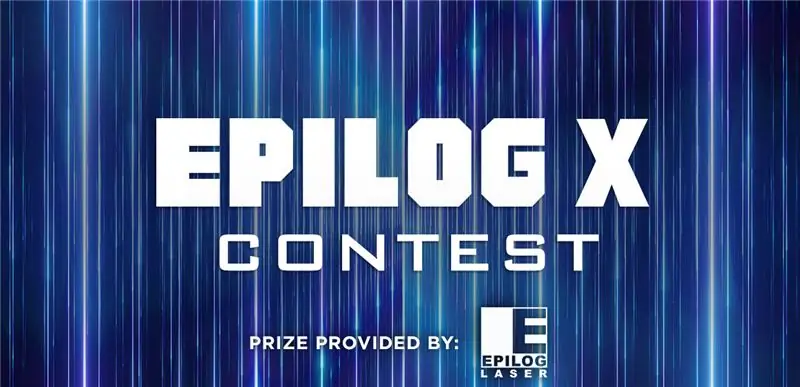
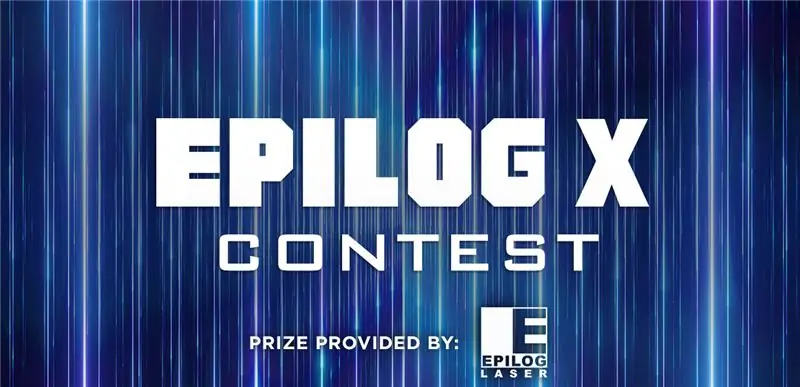
Финалист конкурса Epilog X Contest