Передовая производственная группа CRP известна тем, что использует технологию 3D-печати для производства высокоскоростных транспортных средств, описываемых такими прилагательными, как «супер», таких как их полностью электрический «супербайк» Energic. В своем последнем проекте с Kepler Motors и обладателем мирового рекорда скорости Рассом Уиксом компания применила как 3D-печать, так и расширенные прилагательные к чертежной доске, чтобы создать гиперкар MOTION, автомобиль, спроектированный с использованием оптимизированных компонентов и материалов для достижения максимальной производительности.
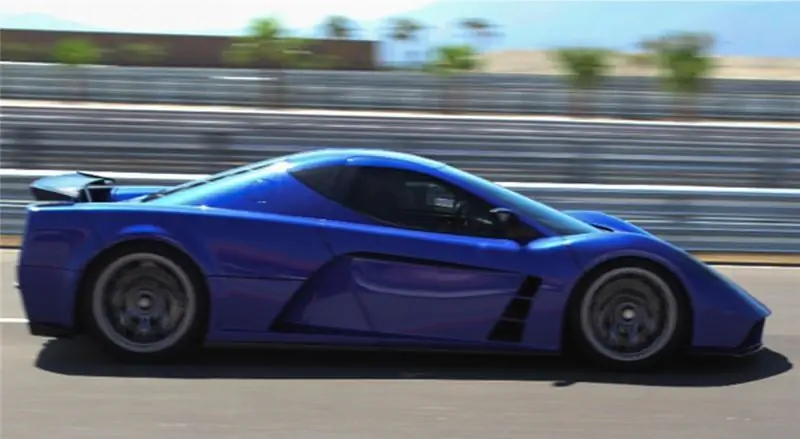
В поисках эксперта по Формуле-1 и 3D-печати компания Kepler Motors обратилась к CRP Group для 3D-печати мелкосерийных деталей для серийных гиперкаров 50 MOTION. Вскоре они поняли, что 3D-печать CRP можно использовать не только для непосредственного изготовления отдельных деталей, но и для создания моделей для литья по выплавляемым моделям. Это позволило Kepler еще больше воспользоваться уникальными возможностями 3D-печати для литья титановых стоек для серии MOTION. Автомобильная компания также смогла использовать технологии CRP для быстрого литья и обработки с ЧПУ для дальнейшего производства своих автомобилей.
Директор по операциям CRP USA Стюарт Дэвис уточнил: «Очень часто компании переосмысливают свой дизайн, как только понимают потенциал 3D-печати. Как только инженер понимает возможность изготовления очень сложных конструкций и форм с использованием технологий и приложений аддитивного производства, форм, которые невозможно изготовить с помощью традиционных процессов, он начинает проектирование без ограничений. Комбинируя 3D-печать, быстрое литье и прецизионную обработку с ЧПУ, инженеры могут мыслить нестандартно, не ограничиваясь традиционными методами производства, и проектировать сложные детали».
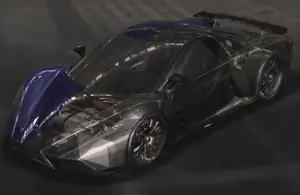
Среди особенностей, уникальных для MOTION, является его двойная трансмиссия, состоящая из 550-сильного двигателя Twin-Turbo V6, который приводит в движение задние колеса отдельно от двух электродвигателей, подключенных к передней части, что позволяет гиперкару достичь 800 лошадиных сил. Благодаря этому MOTION может разгоняться от 0 до 60 миль в час менее чем за 2,5 секунды и достигать скорости более 320 миль в час. Шасси и кузов MOTION состоят из композитного монокока из углеродного волокна. Чтобы гарантировать, что MOTION сможет выдержать физические нагрузки, к конструкции автомобиля был применен анализ методом конечных элементов (FEA), который виртуально моделировал различные сценарии нагрузки перед созданием некоторых частей автомобиля. В результате двойные поперечные рычаги в стиле F1, два наиболее сложных и важных компонента автомобиля, были оптимально спроектированы для соединения с колесами через титановые стойки, составляющие систему подвески с толкателями. Таким образом, сложные стойки подвески были спроектированы и изготовлены таким образом, чтобы они были максимально легкими, и в то же время давали MOTION возможность выдерживать различные нагрузки.
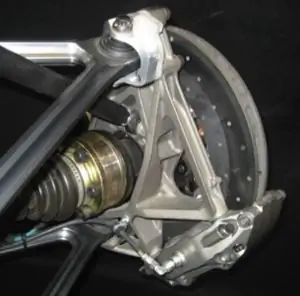
Расс Уикс, основатель Kepler Motors, объяснил, почему титановые стойки и 3D-печать, использованная для их литья, имеют решающее значение для дизайна и характеристик автомобиля: «Легкость, прочность и долговечность имеют важное значение для гиперкар для достижения своей производительности. Литой титан - передовая технология для этого приложения, которое для Kepler MOTION было единственным выбором. В других автомобилях для этого применения используется литой алюминий или заготовка, что делает их громоздкими, слабыми и тяжелыми. Обычно для стоек используется алюминий, а толщина материала увеличивается, что снижает гибкость конструкции. Из-за увеличенной толщины материала точность обработки имеет решающее значение для обеспечения правильного положения компонентов, а также сложных углов обрабатываемых поверхностей. Это делает обработку с ЧПУ обязательной, но может ограничить наше дизайнерское творчество. Работа с CRP Meccanica позволила нам оптимизировать процесс. Использование их технологии аддитивного производства лазерного спекания для 3D-печати шаблона для отливки стойки из титана позволило нам разработать оптимальную легкую и прочную деталь без каких-либо компромиссов. CRP Meccanica управляла всем производственным процессом - от дизайна до готовой детали. Они доставили распечатанные на 3D-принтере модели стоек в литейный цех, отлили их из титана, прецизионно обработали титановые стойки с ЧПУ, провели анализ методом конечных элементов и проверили готовые стойки. Результаты оказались лучше, чем мы могли себе представить».
CRP Group становится важным игроком в области автоспорта, космоса, обороны и автомобилестроения, поскольку у них есть возможность применять технологию 3D-печати и их высокоэффективные материалы для проектирования критически важных составные части. По этой причине технический директор Kepler Derk Hartland считает, что CRP является подходящим партнером для проекта: «Мы сотрудничаем с CRP Group и их сетью компаний, потому что они являются экспертами в F1 и знают, как применять аддитивное производство к общей конструкции. процесс. Возможность использовать знания Стюарта Дэвиса и его команды имела решающее значение для переосмысления того, как мы проектировали нашу стойку. CRP Meccanica была ключевой частью нашего процесса проектирования», - сказал Хартланд. «Литье из титана - это искусство, и для создания оптимальной детали требуются знания и опыт. Компании CRP Group были очень любезны, профессиональны и с ними было приятно работать на протяжении всего проекта».
При разработке таких транспортных средств, как гиперкар MOTION, CRP демонстрирует, что, даже если 3D-печать не используется для прямого производства компонентов, она может играть жизненно важную роль, помогая традиционным методам производства создавать сложные компоненты..